Multi-mode failure judgment method suitable for transverse isotropic carbon fibers
A technology of transversely isotropic and isotropic carbon fibers, which is applied in special data processing applications, instruments, electrical digital data processing, etc., can solve the problems of not considering the influence of the failure state and not being applicable, so as to improve the prediction accuracy and facilitate the program The effect of simple code and derivation process
- Summary
- Abstract
- Description
- Claims
- Application Information
AI Technical Summary
Problems solved by technology
Method used
Image
Examples
Embodiment Construction
[0041] The implementation of the multi-mode failure determination method for transversely isotropic carbon fibers involved in the present invention will be described below in conjunction with the accompanying drawings and specific calculation examples.
[0042] A multi-mode failure judgment method for transversely isotropic carbon fibers. It is characterized in that it not only distinguishes the failure stress state when the fiber is sheared and bent, but also considers the specific influence of the normal stress sign of the failure surface on the failure stress state in each mode, so that the transversely isotropic carbon fiber can be analyzed. The failure of the mode can be accurately judged.
[0043] The concrete steps of invented method are as follows:
[0044] Step 1: Construct the basic type of shear and bending failure stress criteria for transversely isotropic fibers.
[0045] Assuming that the carbon fiber 2-3 plane is an isotropic plane and the 1 direction is the a...
PUM
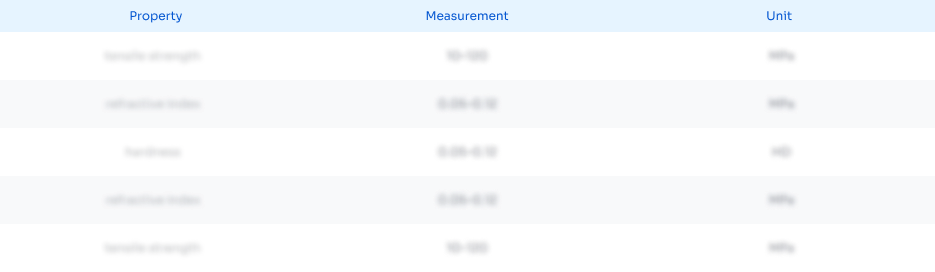
Abstract
Description
Claims
Application Information

- R&D
- Intellectual Property
- Life Sciences
- Materials
- Tech Scout
- Unparalleled Data Quality
- Higher Quality Content
- 60% Fewer Hallucinations
Browse by: Latest US Patents, China's latest patents, Technical Efficacy Thesaurus, Application Domain, Technology Topic, Popular Technical Reports.
© 2025 PatSnap. All rights reserved.Legal|Privacy policy|Modern Slavery Act Transparency Statement|Sitemap|About US| Contact US: help@patsnap.com