Linear oscillation motor sensorless control method and device
An oscillating motor and control method technology, which is applied in the direction of motor generator control, AC motor control, and electromechanical transmission control, can solve problems such as increasing system volume, reducing overall reliability, and difficult installation of position sensors, and achieves displacement estimation. High precision, weaken chattering problem, and improve the effect of displacement observation effect
- Summary
- Abstract
- Description
- Claims
- Application Information
AI Technical Summary
Problems solved by technology
Method used
Image
Examples
Embodiment
[0146] Taking the stator permanent magnet double-stator linear oscillation motor as an example, the above method is simulated and verified, and the rated power is set to 120W, the rated operating frequency is 22.1Hz, the stator resistance is 18.4Ω, the stator inductance is 0.755H, and the thrust coefficient is 47.08 N / A, the mass of the mover piston is 1.03kg.
[0147] Specifically, Fig. 4(a) and Fig. 4(b) respectively show the speed estimation signals obtained by the traditional open-loop back EMF method and the improved sliding mode observer method under the open-loop amplitude of the linear oscillator motor using a low-pass filter. Filtering results; from Figure 4(a) and Figure 4(b), it can be seen that the low-pass filter will cause displacement estimation signal amplitude and phase offset, and cannot solve the problem of sliding mode chattering; Figure 5(a) and Fig. 5(b) respectively show the traditional open-loop back EMF and the improved slippery current obtained by usi...
PUM
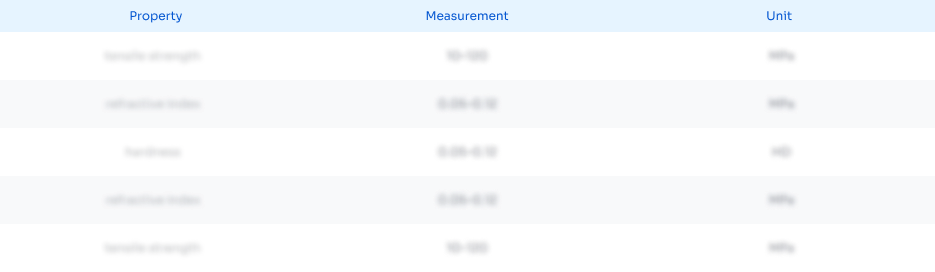
Abstract
Description
Claims
Application Information

- Generate Ideas
- Intellectual Property
- Life Sciences
- Materials
- Tech Scout
- Unparalleled Data Quality
- Higher Quality Content
- 60% Fewer Hallucinations
Browse by: Latest US Patents, China's latest patents, Technical Efficacy Thesaurus, Application Domain, Technology Topic, Popular Technical Reports.
© 2025 PatSnap. All rights reserved.Legal|Privacy policy|Modern Slavery Act Transparency Statement|Sitemap|About US| Contact US: help@patsnap.com