High-elasticity flax fabric and preparation process thereof
A preparation process and high-elasticity technology, applied in bacterial retting, rayon manufacturing, textile, etc., can solve the problem that the rebound performance of the covered yarn is not fully divergent, achieve stable bonding, improve rebound ability, Breathable and smooth effect
- Summary
- Abstract
- Description
- Claims
- Application Information
AI Technical Summary
Problems solved by technology
Method used
Image
Examples
Embodiment 1
[0027] like Figure 1 to 3 Illustrated, a highly elastic linen fabrics, the fabric covering yarn is woven from linen; Linen said corespun yarn comprising a spandex fiber layer 2, an adhesive 3 spinning, flax fiber layer 4; the spandex fiber layer 2 a hollow internal structure 21; a plurality of uniformly disposed spandex spun bonded fibrous outer layer 2, 3 four weeks; 3 is provided with strip-shaped gap 31 between the adhesive spinning; spinning the adhesive 3 four weeks flax fiber layer 4 disposed outside; component, and 3 parts by weight of the adhesive spinning as follows: 50 parts of an epoxy resin, 20 parts of plasticizer, 5 parts of dispersing agent, 5 parts of urethane. Further, the plasticizer is a plasticizer DOP. Further, the dispersing agent is a polyacrylamide.
Embodiment 2
[0029] like Figure 1 to 3 Illustrated, a highly elastic linen fabrics, the fabric covering yarn is woven from linen; Linen said corespun yarn comprising a spandex fiber layer 2, an adhesive 3 spinning, flax fiber layer 4; the spandex fiber layer 2 a hollow internal structure 21; a plurality of uniformly disposed spandex spun bonded fibrous outer layer 2, 3 four weeks; 3 is provided with strip-shaped gap 31 between the adhesive spinning; spinning the adhesive 3 flax fiber set around the outer layer 4; parts by weight of the adhesive component, and spinning are as follows: 55 parts of an epoxy resin, 25 parts plasticizer, 80 parts of a dispersant, 10 parts of urethane. Further, the plasticizer is a plasticizer DOP. Further, the dispersing agent is a polyacrylamide.
Embodiment 3
[0031] like Figure 1 to 3 Illustrated, a highly elastic linen fabrics, the fabric covering yarn is woven from linen; Linen said corespun yarn comprising a spandex fiber layer 2, an adhesive 3 spinning, flax fiber layer 4; the spandex fiber layer 2 a hollow internal structure 21; a plurality of uniformly disposed spandex spun bonded fibrous outer layer 2, 3 four weeks; 3 is provided with strip-shaped gap 31 between the adhesive spinning; spinning the adhesive 3 flax fiber set around the outer layer 4; component, and 3 parts by weight of the adhesive spinning are as follows: 55 parts of an epoxy resin, 25 parts plasticizer, 7 parts of a dispersing agent, 7 parts of urethane. Further, the plasticizer is a plasticizer DOP. Further, the dispersing agent is a polyacrylamide.
PUM
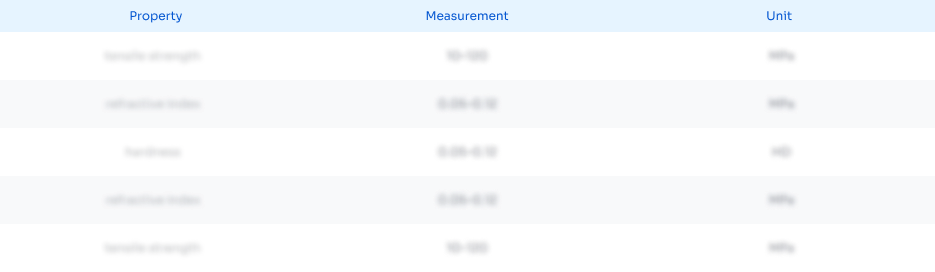
Abstract
Description
Claims
Application Information

- R&D Engineer
- R&D Manager
- IP Professional
- Industry Leading Data Capabilities
- Powerful AI technology
- Patent DNA Extraction
Browse by: Latest US Patents, China's latest patents, Technical Efficacy Thesaurus, Application Domain, Technology Topic, Popular Technical Reports.
© 2024 PatSnap. All rights reserved.Legal|Privacy policy|Modern Slavery Act Transparency Statement|Sitemap|About US| Contact US: help@patsnap.com