Method for continuously producing chloroethane
A technology of ethyl chloride and ethanol, which is applied in the field of continuous production of ethyl chloride, can solve the problems of large equipment volume, low reaction efficiency, high energy consumption of waste water, etc., achieve small device volume, reduce reaction temperature, and reduce production equipment costs Effect
- Summary
- Abstract
- Description
- Claims
- Application Information
AI Technical Summary
Problems solved by technology
Method used
Image
Examples
Embodiment 1
[0074]Configure aluminum chloride-zinc chloride-hydrochloric acid solution in the 5-party circulating liquid receiving tank, wherein the mass ratio of aluminum chloride:zinc chloride is 1:2; the hydrogen chloride content in the solution is 10%; aluminum chloride-zinc chloride The total content is 30%. Turn on the hypergravity reactor and hypergravity refining equipment, and the speed is controlled at 500r / min. The circulating pump P is turned on to circulate the composite catalyst system solution, and the temperature is raised to 115-120° C. through the circulating liquid heat exchanger A. Turn on the concentrated hydrochloric acid analysis device, feed 31% concentrated hydrochloric acid, control the flow rate at 7600kg / h, control the analysis temperature at 125-130°C, and monitor and feed the hydrogen chloride gas generated with a flow meter, and the feed rate is 1070kg / h. The liquid ethanol is heated in the plate heat exchanger, converted into ethanol gas and started to fee...
Embodiment 2
[0082] Configure aluminum chloride-zinc chloride-hydrochloric acid solution in the 5-party circulating liquid receiving tank, wherein the mass ratio of aluminum chloride:zinc chloride is 1:2.5; the hydrogen chloride content in the solution is 10%; aluminum chloride-zinc chloride The total content is 40%. Turn on the hypergravity reactor and hypergravity refining equipment, and the speed is controlled at 500r / min. The circulating pump P is turned on to circulate the composite catalyst system solution, and the temperature is raised to 120-125° C. through the circulating liquid heat exchanger A. Turn on the concentrated hydrochloric acid analysis device, feed 31% concentrated hydrochloric acid, control the flow rate at 6600kg / h, control the analysis temperature at 130-135°C, and monitor the feed of hydrogen chloride gas with a flow meter, and the feed rate is 1070kg / h. The liquid ethanol is heated in the plate heat exchanger, converted into ethanol gas and started to feed, where...
Embodiment 3
[0084] Configure aluminum chloride-zinc chloride-hydrochloric acid solution in the 5-party circulating liquid receiving tank, wherein the mass ratio of aluminum chloride:zinc chloride is 1:3; the hydrogen chloride content in the solution is 15%; aluminum chloride-zinc chloride The total content is 50%. Turn on the hypergravity reactor and hypergravity refining equipment, and the speed is controlled at 500r / min. The circulating pump P is turned on to circulate the composite catalyst system solution, and the temperature is raised to 125-130° C. through the circulating liquid heat exchanger A. Turn on the concentrated hydrochloric acid analysis device, feed 31% concentrated hydrochloric acid, control the flow rate at 6500kg / h, control the analysis temperature at 135-140°C, and monitor and feed the hydrogen chloride gas generated by a flow meter, and the feed rate is 1070kg / h. The liquid ethanol is heated in the plate heat exchanger, converted into ethanol gas and started to feed...
PUM
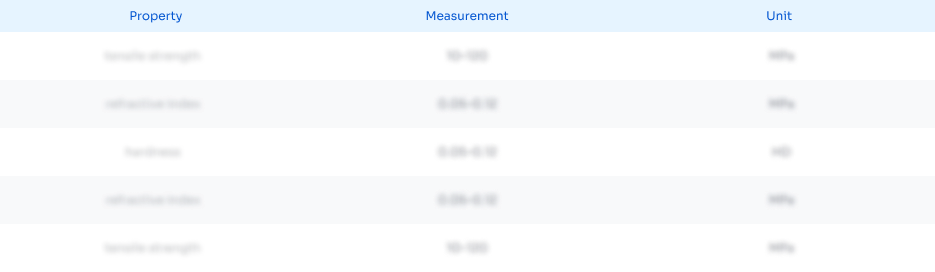
Abstract
Description
Claims
Application Information

- Generate Ideas
- Intellectual Property
- Life Sciences
- Materials
- Tech Scout
- Unparalleled Data Quality
- Higher Quality Content
- 60% Fewer Hallucinations
Browse by: Latest US Patents, China's latest patents, Technical Efficacy Thesaurus, Application Domain, Technology Topic, Popular Technical Reports.
© 2025 PatSnap. All rights reserved.Legal|Privacy policy|Modern Slavery Act Transparency Statement|Sitemap|About US| Contact US: help@patsnap.com