Size maximization rapid cutting method for steel plate in abnormal rolling state
A kind of abnormal state, fast cutting technology, applied in the field of metallurgical steel plate cutting, can solve the problems of insufficient width, too many limit specifications, increased cost and so on
- Summary
- Abstract
- Description
- Claims
- Application Information
AI Technical Summary
Problems solved by technology
Method used
Image
Examples
Embodiment 1
[0063] In a night shift, a piece of steel plate with incoming material size 12*2880*15280mm was found in the fire cutting site, and the contract size was: 12*2800*15200mm. Due to the serious camber of rolling, according to the normal cutting form, the effective size of the fire cutting can only be cut out to 12mm. *2610*15200mm, the steel plate cannot meet the contract size, it needs to be removed from the contract and changed to the length by fire cutting. By optimizing the fire cutting cutting form, the spring line method is carried out according to the steps of determining the position of the steel plate spring line. The cutting size is: 12*2870*15370mm, Since the contract size is: 12*2800*15200mm, the steel plate should be cut in the effective size. It can be seen that through the application of the present invention: the maximum cutting of the steel plate under the abnormal situation of the rolling incoming material is solved, and the utilization rate of the finished produ...
PUM
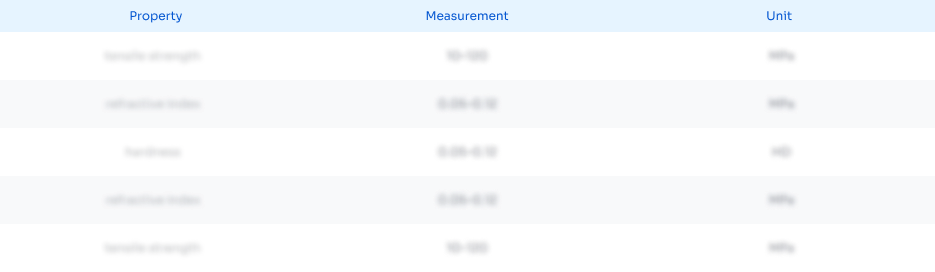
Abstract
Description
Claims
Application Information

- R&D Engineer
- R&D Manager
- IP Professional
- Industry Leading Data Capabilities
- Powerful AI technology
- Patent DNA Extraction
Browse by: Latest US Patents, China's latest patents, Technical Efficacy Thesaurus, Application Domain, Technology Topic, Popular Technical Reports.
© 2024 PatSnap. All rights reserved.Legal|Privacy policy|Modern Slavery Act Transparency Statement|Sitemap|About US| Contact US: help@patsnap.com