Split type DM inner layer oil seal part machining method
A part processing, split-type technology, which is applied in the field of oil seal processing, can solve the problems of clamping internal stress, lack of processing experience, and increase in the gap between the middle split surfaces, etc., to achieve stable processing methods, avoid clamping internal stress, and improve flatness Effect
- Summary
- Abstract
- Description
- Claims
- Application Information
AI Technical Summary
Problems solved by technology
Method used
Image
Examples
Embodiment Construction
[0064] Theoretical basis
[0065] a. After the part is cut in half, there will be a large amount of residual stress inside the part, which will cause the part to deform with the release of internal stress after the part is processed, so that the mid-plane gap of the part will increase and the size, Form and position tolerances and other out-of-tolerance.
[0066] b. After the part is cut in half, add a heat treatment process to anneal the part to release the stress inside the part, but the release of stress will cause the deformation of the positioning surface, making the positioning surface uneven during grinding. is not meeting the requirements.
[0067] c. After the internal stress of the positioning surface is released, a certain deformation will occur, resulting in the flatness of the positioning surface not meeting the requirements. Before machining, the part needs to be clamped based on the positioning surface, and the runout of the centering surface should not exceed...
PUM
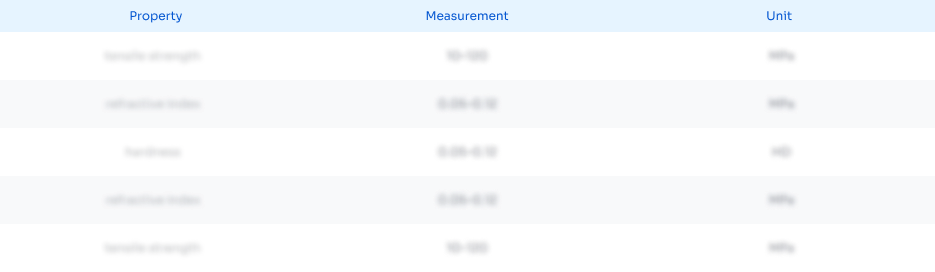
Abstract
Description
Claims
Application Information

- R&D Engineer
- R&D Manager
- IP Professional
- Industry Leading Data Capabilities
- Powerful AI technology
- Patent DNA Extraction
Browse by: Latest US Patents, China's latest patents, Technical Efficacy Thesaurus, Application Domain, Technology Topic, Popular Technical Reports.
© 2024 PatSnap. All rights reserved.Legal|Privacy policy|Modern Slavery Act Transparency Statement|Sitemap|About US| Contact US: help@patsnap.com