Micro-channel reactor manufactured based on 3D printer technology
A micro-channel reactor, 3D printer technology, applied in chemical/physical/physical-chemical reactors, chemical instruments and methods, chemical/physical/physical-chemical processes, etc., can solve problems such as inability to meet, unreasonable utilization of processing materials, etc. , to reduce energy consumption, increase the reaction contact area and duration, and promote effective progress
- Summary
- Abstract
- Description
- Claims
- Application Information
AI Technical Summary
Problems solved by technology
Method used
Image
Examples
Embodiment Construction
[0026] The specific content of the present invention is further described below:
[0027] The invention is a micro-channel reactor manufactured based on 3D printer technology, which is composed of a plurality of micro-reaction channel module units printed by 3D technology.
[0028] The microreactor module unit of the present invention is square body, as image 3 and Figure 4 As shown, there are many regularly arranged microchannel reaction tubes embedded in the microreactor module unit, and the microchannel reaction tube can be integrated with the microreactor module unit, or the microreactor module unit can be embedded in the microreactor module unit Inside.
[0029] Microchannel reaction tube structure such as figure 1 As shown, it includes an inner heat exchange medium cavity 1 , a material reaction cavity 2 and a surrounding heat exchange medium cavity 3 .
[0030] Such as figure 1 As shown, the inner layer heat exchange medium cavity 1 is located in the central posi...
PUM
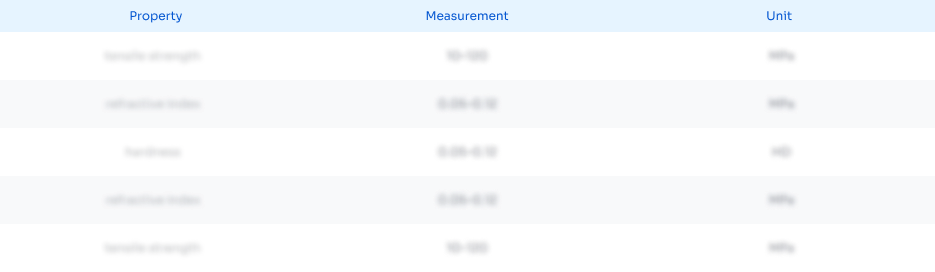
Abstract
Description
Claims
Application Information

- R&D
- Intellectual Property
- Life Sciences
- Materials
- Tech Scout
- Unparalleled Data Quality
- Higher Quality Content
- 60% Fewer Hallucinations
Browse by: Latest US Patents, China's latest patents, Technical Efficacy Thesaurus, Application Domain, Technology Topic, Popular Technical Reports.
© 2025 PatSnap. All rights reserved.Legal|Privacy policy|Modern Slavery Act Transparency Statement|Sitemap|About US| Contact US: help@patsnap.com