Method for producing aromatic hydrocarbons and/or liquid fuels from light hydrocarbons
A liquid fuel and light hydrocarbon technology, applied in chemical instruments and methods, liquid hydrocarbon mixture production, bulk chemical production, etc., can solve the problems of easy catalyst deactivation, low carbon utilization rate, catalyst deactivation, etc., and achieve process design Simple operation, high carbon utilization rate, long catalyst life effect
- Summary
- Abstract
- Description
- Claims
- Application Information
AI Technical Summary
Problems solved by technology
Method used
Image
Examples
Embodiment 1
[0074] use figure 1 The process shown, the volume ratio of 1.67:1 C 2 h 6 / N 2 The mixed gas is sent to the two reactors of dehydrogenation and oligomerization / aromatization in series, the dehydrogenation temperature is set at 750°C, and the GHSV of ethane is 1000h -1 , the pressure is normal pressure, and the reaction is carried out without a catalyst. Under these conditions, the conversion of ethane was about 57%, and the concentration of ethylene in the dehydrogenation product gas stream was about 22% by volume. The set temperatures of oligomerization / aromatization fixed bed reactors are 400°C, 450°C, 500°C and 550°C respectively, WHSV=2.68g-C 2 h 6 / g-cat·hr (equivalent to 1.6g-C 2 h 4 / g-cat·hr), the pressure is normal pressure (1 bar), the catalyst is Ga / ZSM-5 / Al prepared by saturated impregnation method 2 o 3 Catalyst (the content of Ga is 2.0% by weight, and the silicon-aluminum mol ratio of ZSM-5 is 30, and molecular sieve and binder Al 2 o 3 The weight rat...
Embodiment 2
[0091] Different from the method of Example 1, use the mixture gas stream that is formulated according to the product composition of step 1) in Example 1, and its composition and volume ratio are C 2 h 4 / H 2 / N 2 =1:1:1. The catalyst is the same as the catalyst for oligomerization / aromatization in Example 1, that is, Ga / ZSM-5 / Al prepared by saturated impregnation method 2 o 3 Catalyst (the content of Ga is 2.0% by weight, and the silicon-aluminum mol ratio of ZSM-5 is 30, and molecular sieve and binder Al 2 o 3 The weight ratio is 82.5 / 17.5). The conditions of aromatization are 450°C and 550°C, normal pressure, WHSV=0.75g-C 2 h 4 / g-cat·hr, the reaction time is 6 hours. The results of the 6-hour average BTX yield and product selectivity calculated on the basis of ethylene are shown in Table 2.
Embodiment 4
[0095] The experiment was carried out according to the method of Example 2, except that the catalyst used for ethylene aromatization was ZSM-5 containing 1% nickel by the total weight of molecular sieves (ZSM-5 was the same as in Example 1). The average results of the reaction at 450°C for 6 hours are shown in Table 2.
PUM
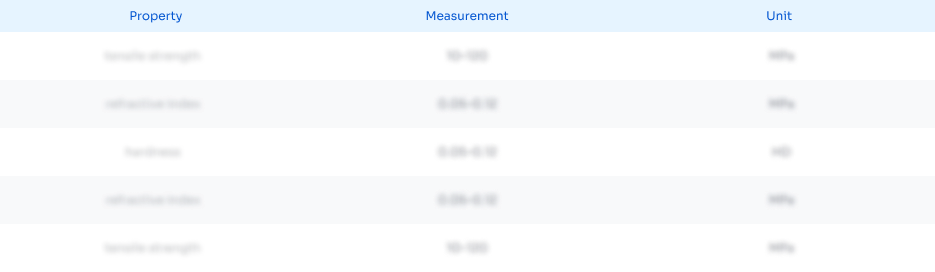
Abstract
Description
Claims
Application Information

- Generate Ideas
- Intellectual Property
- Life Sciences
- Materials
- Tech Scout
- Unparalleled Data Quality
- Higher Quality Content
- 60% Fewer Hallucinations
Browse by: Latest US Patents, China's latest patents, Technical Efficacy Thesaurus, Application Domain, Technology Topic, Popular Technical Reports.
© 2025 PatSnap. All rights reserved.Legal|Privacy policy|Modern Slavery Act Transparency Statement|Sitemap|About US| Contact US: help@patsnap.com