Preparation method of graphene/helical carbon fiber/epoxy resin composite material
A technology of spiral carbon fiber and epoxy resin, which is applied in the chemical characteristics of fibers, textiles and paper making, etc., can solve the problems of affecting electrical conductivity, adverse effects of epoxy resin mechanical properties and electrical conductivity, environmental pollution, etc.
- Summary
- Abstract
- Description
- Claims
- Application Information
AI Technical Summary
Problems solved by technology
Method used
Image
Examples
Embodiment 1
[0029] A preparation method of graphene / spiral carbon fiber / epoxy resin composite material, the method comprising:
[0030] S1, loading the catalyst used to prepare the spiral carbon fiber in the three-dimensional foam to obtain the supported catalyst; specifically,
[0031] S1.1. Under magnetic stirring, slowly add 100mL of 0.02mol / L copper chloride aqueous solution into 100mL of 0.02mol / L potassium sodium tartrate solution, keep stirring for 20min, then filter to obtain a blue precipitate, and alternately use ethanol and distilled water Wash 3 times to obtain copper tartrate; then disperse copper tartrate in water to form a suspension, immerse the washed melamine foam in the suspension, and place it in an oven at 100°C after the melamine foam absorbs the suspension Drying; the dried melamine foam is submerged in the suspension again, and then dried in an oven at 100° C. to obtain a melamine foam loaded with copper tartrate;
[0032] S1.2. Put the melamine foam loaded with c...
Embodiment 2
[0037] A preparation method of graphene / spiral carbon fiber / epoxy resin composite material, the method comprising:
[0038] S1, loading the catalyst used to prepare the spiral carbon fiber in the three-dimensional foam to obtain the supported catalyst; specifically,
[0039]S1.1. Under magnetic stirring, slowly add 100mL of 0.05mol / L copper chloride aqueous solution into 100mL of 0.05mol / L potassium sodium tartrate solution, keep stirring for 40min, filter to obtain blue precipitate, and alternately use ethanol and distilled water Wash 3 times to obtain copper tartrate; then disperse copper tartrate in water to form a suspension, immerse the washed melamine foam in the suspension, and place it in an oven at 80°C after the melamine foam is fully absorbed by the suspension Drying; repeat above-mentioned immersion, dry operation three times, obtain the melamine foam that is loaded with copper tartrate;
[0040] S1.2. Put the melamine foam loaded with copper tartrate in the porce...
Embodiment 3
[0045] A preparation method of graphene / spiral carbon fiber / epoxy resin composite material, the method comprising:
[0046] S1, loading the catalyst used to prepare the spiral carbon fiber in the three-dimensional foam to obtain the supported catalyst; specifically,
[0047] S1.1. Under magnetic stirring, slowly add 100mL of 0.03mol / L copper chloride aqueous solution into 100mL of 0.03mol / L potassium sodium tartrate solution, keep stirring for 20min and then filter to obtain a blue precipitate, and alternately use ethanol and distilled water Wash 3 times to obtain copper tartrate; then disperse copper tartrate in water to form a suspension, immerse the washed melamine foam in the suspension, and put it in an oven at 120°C after the melamine foam absorbs the suspension Drying; the dried melamine foam is submerged in the suspension again, and then dried in an oven at 120° C. to obtain a melamine foam loaded with copper tartrate;
[0048] S1.2. Put the melamine foam loaded with ...
PUM
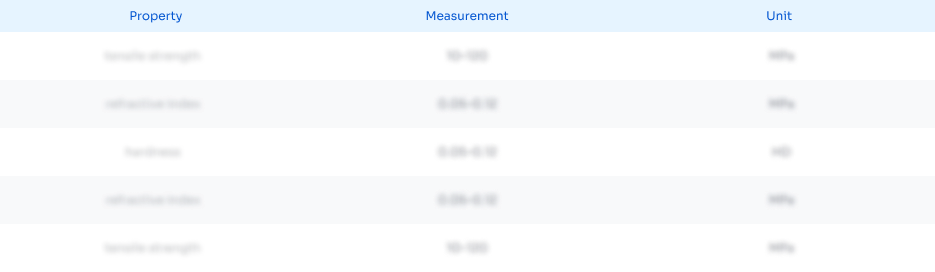
Abstract
Description
Claims
Application Information

- R&D Engineer
- R&D Manager
- IP Professional
- Industry Leading Data Capabilities
- Powerful AI technology
- Patent DNA Extraction
Browse by: Latest US Patents, China's latest patents, Technical Efficacy Thesaurus, Application Domain, Technology Topic, Popular Technical Reports.
© 2024 PatSnap. All rights reserved.Legal|Privacy policy|Modern Slavery Act Transparency Statement|Sitemap|About US| Contact US: help@patsnap.com