Foamed concrete carbon sequestration method
A technology of foamed concrete and carbon sequestration, applied in the field of foamed concrete, can solve the problems of high energy consumption, high cost of carbon sequestration of foamed concrete bricks, complicated process and process, etc.
- Summary
- Abstract
- Description
- Claims
- Application Information
AI Technical Summary
Problems solved by technology
Method used
Image
Examples
Embodiment 1
[0033] A method for sequestering carbon in foamed concrete, comprising the following steps:
[0034] Step S1: Pulverize 23kg of boiler slag from steelworks, 10kg of ash collected by dust collector, 6kg of fly ash, 4kg of desulfurized gypsum and mix with 3kg of cement, add 41kg of mixed raw materials and 100kg of hot water at 40°C into a mixer and stir Obtain hot slurry, in which hot water is obtained by heating steam or flue gas waste heat generated during the power generation process of the thermal power unit or the steelmaking process of the steelmaking plant, which can effectively realize the utilization of heat energy and reduce the cost of energy consumption. Utilize boiler slag, fly ash, dedusting solid waste, desulfurized gypsum, and solid waste to greatly reduce the cost of raw materials for foamed concrete bricks, and realize the recycling and harmless utilization of solid waste;
[0035] Step S2: Into the hot slurry in the mixer, feed the clean flue gas, wherein the ...
Embodiment 2
[0040] A method for sequestering carbon in foamed concrete, comprising the following steps:
[0041] Step S1: Mix 45kg, boiler slag in the thermal power unit, 20kg of ash collected by the dust collector, 11kg of fly ash, 8kg of desulfurized gypsum with 8kg of cement, and add 53kg of mixed raw materials and 100kg of hot water at 80°C to the mixer Stir to obtain hot slurry, in which hot water is obtained by heating steam or flue gas waste heat generated during the power generation process of the thermal power unit or the steelmaking process of the steelmaking plant;
[0042]Step S2: pass into the clean flue gas in the hot slurry in the mixer, wherein the concentration of the clean flue gas in the mixer is 35%, so that the CO in the clean flue gas 2 Reacting with hot slurry, the net flue gas is obtained from at least a part of the flue gas produced in the power plant boiler of the thermal power unit or the blast furnace of the steelmaking plant after desulfurization, denitrificat...
Embodiment 3
[0047] A kind of foam concrete carbon sequestration method, comprises following process:
[0048] Step S1: Mix 15kg of calcium carbide furnace slag, 30kg of boiler slag in a thermal power unit, 26kg of ash collected by a dust collector, and 8kg of desulfurized gypsum with 8kg of cement, and add 50kg of mixed raw materials and 100kg of hot water at 75°C to the mixer Stir to obtain hot slurry, in which hot water is obtained by heating steam or flue gas waste heat generated during the power generation process of the thermal power unit or the steelmaking process of the steelmaking plant;
[0049] Step S2: pass into the clean flue gas in the hot slurry in the mixer, wherein the concentration of the clean flue gas in the mixer is 35%, so that the CO in the clean flue gas 2 Reacting with hot slurry, the net flue gas is obtained from at least a part of the flue gas produced in the power plant boiler of the thermal power unit or the blast furnace of the steelmaking plant after desulfur...
PUM
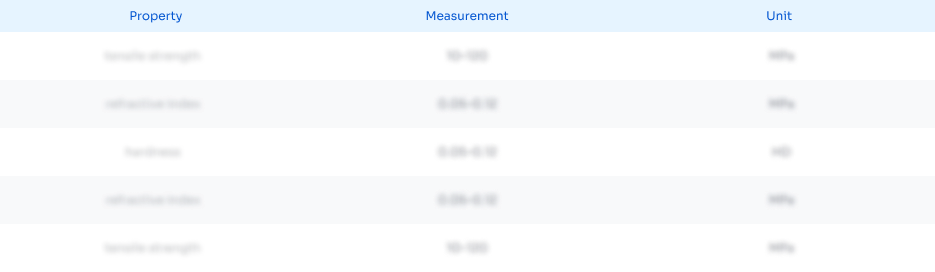
Abstract
Description
Claims
Application Information

- R&D
- Intellectual Property
- Life Sciences
- Materials
- Tech Scout
- Unparalleled Data Quality
- Higher Quality Content
- 60% Fewer Hallucinations
Browse by: Latest US Patents, China's latest patents, Technical Efficacy Thesaurus, Application Domain, Technology Topic, Popular Technical Reports.
© 2025 PatSnap. All rights reserved.Legal|Privacy policy|Modern Slavery Act Transparency Statement|Sitemap|About US| Contact US: help@patsnap.com