High-speed train aluminum alloy supporting groove and preparation method thereof
A technology for high-speed trains and aluminum alloys, applied in the field of aluminum alloys, can solve the problems of unclear evolution law of corrosion damage, increased maintenance costs of high-speed trains, and inability to evaluate the remaining life of components, so as to ensure mechanical strength and ductility, improve Dispersion and precipitation effect, the effect of improving solid solubility
- Summary
- Abstract
- Description
- Claims
- Application Information
AI Technical Summary
Problems solved by technology
Method used
Image
Examples
Embodiment 1
[0024] The high-speed train aluminum alloy support channel aluminum alloy in this embodiment includes the following components in mass percentage: Zn: 5.0wt.%, Mg: 2.0wt.%, Ag: 1.0wt.%, Sc: 0.3wt.%. , Zr: 0.6wt.%, the balance is Al and unavoidable impurities;
[0025] Its preparation method is as follows:
[0026] First, add pure Al, pure Zn, and pure Mg into the melting furnace and heat to 700°C to melt, then add Al-20Ag master alloy and Al-25Sc master alloy after heating up to 720°C; then pass high-purity argon gas, at 730°C Keep it warm for 20 minutes, then add Al-25Zr master alloy and keep it warm for 1 hour, finally cool down to 680°C, let it stand for 15 minutes, and cast it at 660-690°C to make an aluminum alloy ingot. Then the aluminum alloy is homogenized, and the homogenization treatment is to keep warm at 430° C. for 20 hours. Then the obtained aluminum alloy ingot is subjected to low-temperature pre-extrusion, the extrusion temperature is 100 degrees, and the ext...
Embodiment 2
[0028] The high-speed train aluminum alloy support channel aluminum alloy in this embodiment includes the following components in mass percentage: Zn: 6.5wt.%, Mg: 3.0wt.%, Ag: 2.0wt.%, Sc: 0.5wt.%. , Zr: 0.7wt.%, the balance is Al and unavoidable impurities;
[0029] Its preparation method is as follows:
[0030] First, add pure Al, pure Zn, and pure Mg into the melting furnace and heat to 700°C to melt, then add Al-20Ag master alloy and Al-25Sc master alloy after heating up to 720°C; then pass high-purity argon gas, at 730°C Keep it warm for 20 minutes, then add Al-25Zr master alloy and keep it warm for 2 hours, finally cool down to 680°C, let it stand for 15 minutes, and cast it at 660-690°C to make an aluminum alloy ingot. Then the aluminum alloy is homogenized, and the homogenization treatment is to keep warm at 430° C. for 20 hours. Then the obtained aluminum alloy ingot is subjected to low-temperature pre-extrusion, the extrusion temperature is 100 degrees, and the ex...
Embodiment 3
[0032] The high-speed train aluminum alloy support channel aluminum alloy in this embodiment includes the following components in mass percentage: Zn: 7.5wt.%, Mg: 3.5wt.%, Ag: 2.5wt.%, Sc: 0.6wt.%. , Zr: 0.8wt.%, the balance is Al and unavoidable impurities;
[0033] Its preparation method is as follows:
[0034] First, add pure Al, pure Zn, and pure Mg into the melting furnace and heat to 700°C to melt, then add Al-20Ag master alloy and Al-25Sc master alloy after heating up to 720°C; then pass high-purity argon gas, at 730°C Keep it warm for 20 minutes, then add Al-25Zr master alloy and keep it warm for 2 hours, finally cool down to 680°C, let it stand for 15 minutes, and cast it at 660-690°C to make an aluminum alloy ingot. Then the aluminum alloy is homogenized, and the homogenization treatment is to keep warm at 430° C. for 20 hours. Then the obtained aluminum alloy ingot is subjected to low-temperature pre-extrusion, the extrusion temperature is 100 degrees, and the ex...
PUM
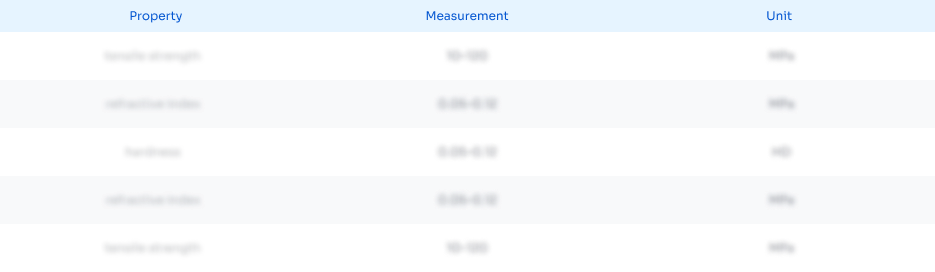
Abstract
Description
Claims
Application Information

- R&D
- Intellectual Property
- Life Sciences
- Materials
- Tech Scout
- Unparalleled Data Quality
- Higher Quality Content
- 60% Fewer Hallucinations
Browse by: Latest US Patents, China's latest patents, Technical Efficacy Thesaurus, Application Domain, Technology Topic, Popular Technical Reports.
© 2025 PatSnap. All rights reserved.Legal|Privacy policy|Modern Slavery Act Transparency Statement|Sitemap|About US| Contact US: help@patsnap.com