Capacitive micro-mechanical accelerometer
A capacitive micro-machine, accelerometer technology, applied in the direction of measurement of acceleration, speed/acceleration/shock measurement, measurement device, etc., can solve problems affecting device stability, accelerometer structure deformation, affecting accelerometer stability, etc.
- Summary
- Abstract
- Description
- Claims
- Application Information
AI Technical Summary
Problems solved by technology
Method used
Image
Examples
Embodiment Construction
[0017] The present invention will be described in detail below in conjunction with the accompanying drawings and embodiments.
[0018] Such as figure 1 In the illustrated embodiment, the accelerometer structures in the present invention are arranged axisymmetrically in the x-direction and y-direction, including anchor points 20A-20B and 30 for fixing the accelerometer movable structure on the substrate 10, and anchor points 20A-20B for fixing the accelerometer. The fixed frame structure 40 on the substrate 10, the sensitive mass frame structure 70, the single-degree-of-freedom elastic beams 60A-60D connecting the fixed frame structure 40 and the sensitive mass frame structure 70, the central anchor point 30 and the sensitive mass The single-degree-of-freedom elastic beams 50A-50D of the block frame structure 70, the detection electrode units 80A-80B, 90A-90B, 100A-100B, etc.
[0019] In the above embodiments, the accelerometer structures are distributed axisymmetrically in th...
PUM
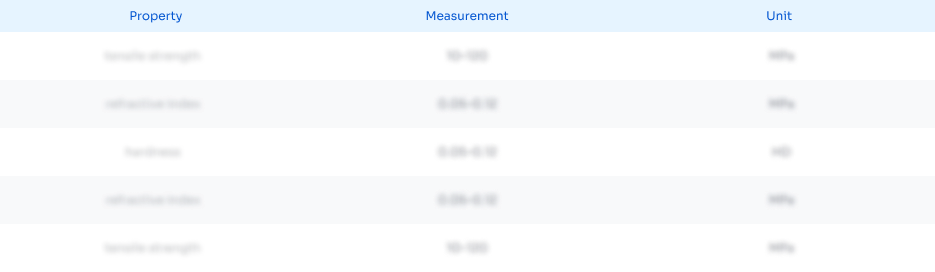
Abstract
Description
Claims
Application Information

- R&D Engineer
- R&D Manager
- IP Professional
- Industry Leading Data Capabilities
- Powerful AI technology
- Patent DNA Extraction
Browse by: Latest US Patents, China's latest patents, Technical Efficacy Thesaurus, Application Domain, Technology Topic, Popular Technical Reports.
© 2024 PatSnap. All rights reserved.Legal|Privacy policy|Modern Slavery Act Transparency Statement|Sitemap|About US| Contact US: help@patsnap.com