Construction method and system of heat conduction model of three-dimensional composite material, terminal and medium
A composite material and construction method technology, which is applied in the field of thermal conductivity analysis and calculation of composite materials, can solve the problems of random distribution of parts that cannot be filled with particles, difficult to realize parts filled with particles, and long time period of thermal conductivity, and achieves fast and efficient research methods, The effect of concise and efficient modeling
- Summary
- Abstract
- Description
- Claims
- Application Information
AI Technical Summary
Problems solved by technology
Method used
Image
Examples
Embodiment
[0088] Example: To study the variation of thermal conductivity of alumina particle-filled epoxy resin matrix composites with particle size and volume fraction.
[0089] Such as figure 1 As shown, the construction method of the thermal conduction model of the three-dimensional composite material provided by the embodiment of the present invention includes the following steps:
[0090] S101, use Python language programming to calculate the epoxy resin RVE model with a specific side length, the number of alumina filler particles with a specific volume fraction and a specific particle size, and create RVE components corresponding to alumina particles and epoxy resin in ABAQUS ;
[0091] S102, using Python language to write a script to realize the assembly of each component and the random distribution of the assembly;
[0092] S103, using the Assembly module and the Material module of the CAE interface of ABAQUS to realize the merging and cutting of the assembly to construct the ...
PUM
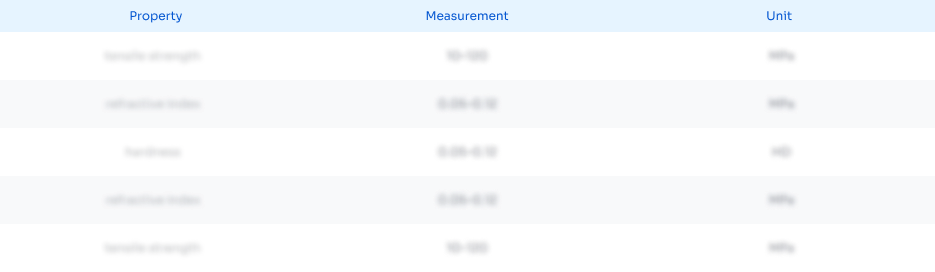
Abstract
Description
Claims
Application Information

- R&D
- Intellectual Property
- Life Sciences
- Materials
- Tech Scout
- Unparalleled Data Quality
- Higher Quality Content
- 60% Fewer Hallucinations
Browse by: Latest US Patents, China's latest patents, Technical Efficacy Thesaurus, Application Domain, Technology Topic, Popular Technical Reports.
© 2025 PatSnap. All rights reserved.Legal|Privacy policy|Modern Slavery Act Transparency Statement|Sitemap|About US| Contact US: help@patsnap.com