Numerical control machine tool rolling bearing fault diagnosis method
A technology for rolling bearings and fault diagnosis, which is applied in complex mathematical operations, data processing applications, testing of mechanical components, etc. It can solve problems such as sampling frequency is greatly affected, affecting parameters, etc., and achieves the effect of improving accuracy and high efficiency
- Summary
- Abstract
- Description
- Claims
- Application Information
AI Technical Summary
Problems solved by technology
Method used
Image
Examples
Embodiment Construction
[0036] The present invention will be described in detail below in conjunction with specific embodiments. The following examples will help those skilled in the art to further understand the present invention, but do not limit the present invention in any form. It should be noted that those skilled in the art can make several modifications and improvements without departing from the concept of the present invention. These all belong to the protection scope of the present invention.
[0037] In the embodiment of the present invention, such as figure 1 As shown, the CNC machine tool rolling bearing fault diagnosis method based on WOA optimized VMD provided by the present invention comprises the following steps:
[0038] Step S1: Collect four vibration signals of the bearings in the headstock, including normal vibration signals of bearings, inner ring fault signals, outer ring fault signals, and rolling element fault signals; The acquisition card is adsorbed on the bearing seat ...
PUM
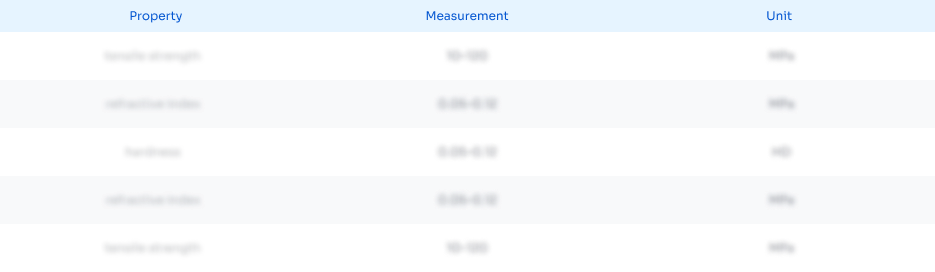
Abstract
Description
Claims
Application Information

- Generate Ideas
- Intellectual Property
- Life Sciences
- Materials
- Tech Scout
- Unparalleled Data Quality
- Higher Quality Content
- 60% Fewer Hallucinations
Browse by: Latest US Patents, China's latest patents, Technical Efficacy Thesaurus, Application Domain, Technology Topic, Popular Technical Reports.
© 2025 PatSnap. All rights reserved.Legal|Privacy policy|Modern Slavery Act Transparency Statement|Sitemap|About US| Contact US: help@patsnap.com