A positioning mechanism for a manipulator of a rotary filling machine
A positioning mechanism and filling machine technology, applied in the field of manipulators, can solve problems such as failure of capping operation, poor positioning effect of manipulators, shaking of material bottles, etc., and achieve better positioning effect, better capping effect, and better stability. Effect
- Summary
- Abstract
- Description
- Claims
- Application Information
AI Technical Summary
Problems solved by technology
Method used
Image
Examples
Embodiment Construction
[0028] The following will clearly and completely describe the technical solutions in the embodiments of the present invention with reference to the accompanying drawings in the embodiments of the present invention. Obviously, the described embodiments are only some, not all, embodiments of the present invention. Based on the embodiments of the present invention, all other embodiments obtained by persons of ordinary skill in the art without making creative efforts belong to the protection scope of the present invention.
[0029] see Figure 1 to Figure 9 , the present invention provides a technical solution: a manipulator positioning mechanism for a rotary filling machine, which includes a rotary table 1 and a support block 13, and also includes a material bottle 11. The upper surface of the rotary table 1 is provided with a groove 2, Each groove 2 corresponds to a manipulator positioning mechanism, and only a single one is drawn in the figure, in order to observe the motion fo...
PUM
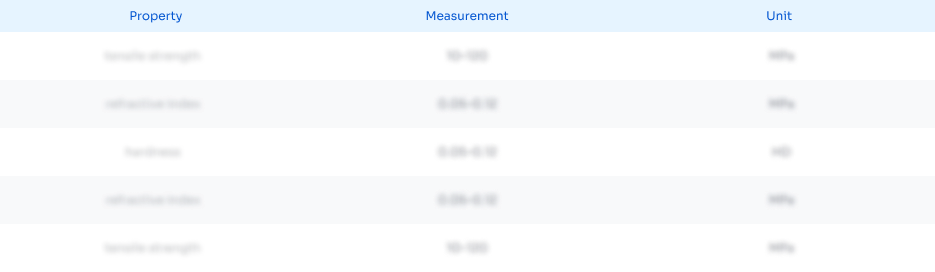
Abstract
Description
Claims
Application Information

- R&D
- Intellectual Property
- Life Sciences
- Materials
- Tech Scout
- Unparalleled Data Quality
- Higher Quality Content
- 60% Fewer Hallucinations
Browse by: Latest US Patents, China's latest patents, Technical Efficacy Thesaurus, Application Domain, Technology Topic, Popular Technical Reports.
© 2025 PatSnap. All rights reserved.Legal|Privacy policy|Modern Slavery Act Transparency Statement|Sitemap|About US| Contact US: help@patsnap.com