Camera calibration device and method for microscopic three-dimensional shape measurement system
A camera calibration and measurement system technology, which is applied in the field of three-dimensional microscopic shape measurement, can solve the problems of loss of measurement accuracy, inaccurate calibration target positioning, lens distortion perspective, etc., to achieve improved extraction accuracy, high robustness, and improved accuracy Effect
- Summary
- Abstract
- Description
- Claims
- Application Information
AI Technical Summary
Problems solved by technology
Method used
Image
Examples
Embodiment 1
[0043] like figure 2 Shown, build workbench, video camera that telecentric lens is housed, control unit, calculation unit, also have digital display device, the used calculation unit of present embodiment is computer, and digital display device is LCD display screen; Digital display device is used for The active target generated by the simulation is displayed, and the calculation unit is a computer, which is used to execute the calibration method described in this embodiment.
[0044] In this field, after the active target is photographed, the photographed picture obtained is called a calibration picture.
[0045] A camera calibration method for a microscopic three-dimensional shape measurement system, comprising the following steps:
[0046]S0, using the simulation algorithm to generate an active target, the active target displays a center feature point, that is, a circular phase shift fringe, the specific method is as follows:
[0047] like image 3 As shown in the upper...
Embodiment 2
[0089] like figure 1 As shown, a microscopic measurement system based on orthographic projection and phase circle target is constructed, including: a three-dimensional microscopic measurement system, and a phase target displayed by LCD. Wherein, the three-dimensional microscopic measurement system includes a workbench, an optical fiber lighting source, a digital micromirror (DMD), a camera, and a computer, and the camera has been calibrated using the calibration device and method of Embodiment 1;
PUM
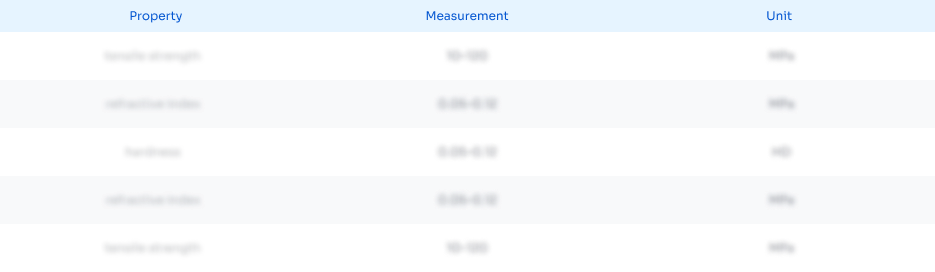
Abstract
Description
Claims
Application Information

- R&D
- Intellectual Property
- Life Sciences
- Materials
- Tech Scout
- Unparalleled Data Quality
- Higher Quality Content
- 60% Fewer Hallucinations
Browse by: Latest US Patents, China's latest patents, Technical Efficacy Thesaurus, Application Domain, Technology Topic, Popular Technical Reports.
© 2025 PatSnap. All rights reserved.Legal|Privacy policy|Modern Slavery Act Transparency Statement|Sitemap|About US| Contact US: help@patsnap.com