Honeycomb plate production and forming composite processing machine
A composite processing, honeycomb panel technology, applied in the direction of cardboard articles, etc., can solve the problems of increased deformation of the honeycomb core, prone to offset, deformation of the honeycomb core, etc., to improve the molding quality, reduce the probability of deformation, and reduce movement. The effect of resistance
- Summary
- Abstract
- Description
- Claims
- Application Information
AI Technical Summary
Problems solved by technology
Method used
Image
Examples
Embodiment Construction
[0029] The technical solutions in the embodiments of the present invention will be clearly and completely described below in conjunction with the accompanying drawings in the embodiments of the present invention. Obviously, the described embodiments are only some of the embodiments of the present invention, not all of them; based on The embodiments of the present invention and all other embodiments obtained by persons of ordinary skill in the art without making creative efforts belong to the protection scope of the present invention.
[0030] refer to Figure 1-8 , a compound processing machine for producing and forming honeycomb panels, comprising a clamping mechanism 1 and a pressing mechanism 2, the clamping mechanism 1 is placed on the ground, and the left end of the clamping mechanism 1 is arranged with the pressing mechanism 2.
[0031] refer to figure 1 , figure 2 , image 3 with Figure 7 , the clamping mechanism 1 includes a stand 10, a disc 11, a No. 1 electric ...
PUM
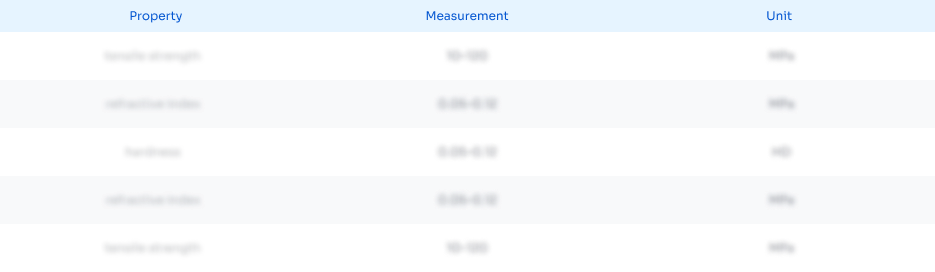
Abstract
Description
Claims
Application Information

- R&D
- Intellectual Property
- Life Sciences
- Materials
- Tech Scout
- Unparalleled Data Quality
- Higher Quality Content
- 60% Fewer Hallucinations
Browse by: Latest US Patents, China's latest patents, Technical Efficacy Thesaurus, Application Domain, Technology Topic, Popular Technical Reports.
© 2025 PatSnap. All rights reserved.Legal|Privacy policy|Modern Slavery Act Transparency Statement|Sitemap|About US| Contact US: help@patsnap.com