Method for preparing hollow integral structure by using pipes
An overall structure, hollow technology, applied in the direction of mechanical equipment, engine components, etc., can solve the problems of increasing the number and complexity of hot pressing molds, and achieve the effect of reducing the difficulty of processing technology, avoiding the defects of gas ports between core plates, and being easy to achieve
- Summary
- Abstract
- Description
- Claims
- Application Information
AI Technical Summary
Problems solved by technology
Method used
Image
Examples
Embodiment 1
[0064] Example as Figure 1-8 As shown, the hollow structure includes at least one layer of a tube array, the tube array includes a number of tubes 2 parallel to each other and closely arranged in sequence, and the upper and lower sides of the tube array are provided with panels 4 with flat panels. 4. It is fixedly connected to several tubes 2 in the tube array; because the structure is tube 2 before forming, it can reduce the superplastic forming process of the core board, and can directly heat and pressurize the diffusion, which can reduce the difficulty of the processing technology and avoid the use of existing There are defects such as gas port defects between core plates caused by the multi-layer plate forming process, diffusion welding defects between core plates, and the inability of the core plates to fully expand to form a rectangular cross-sectional shape.
[0065] When the panel is a flat plate, the hollow structure is prepared as follows:
[0066] S1 blank prepara...
Embodiment example 2
[0100] Implementation case two such as figure 1 and 9 As shown in -12, the tube array includes a number of tubes 2 that are parallel to each other and closely arranged in sequence. The inner and outer sides of the tube array are provided with cylindrical thin-walled panels 9 whose panels are cylindrical thin-walled tubes. The thin-walled panel 9 is fixedly connected to several tubes 2 in the tube array; because the structure is a tube structure before forming, the superplastic forming process of the core plate can be reduced, and the direct heating and pressure diffusion can be performed, which can reduce the difficulty of the processing technology and avoid the The existing multi-layer board forming process causes the defects of air ports between the core boards, the diffusion welding defects between the core boards, and the inability of the core boards to fully expand to form a rectangular cross-sectional shape and other defects.
[0101] When the panel is a cylindrical thi...
PUM
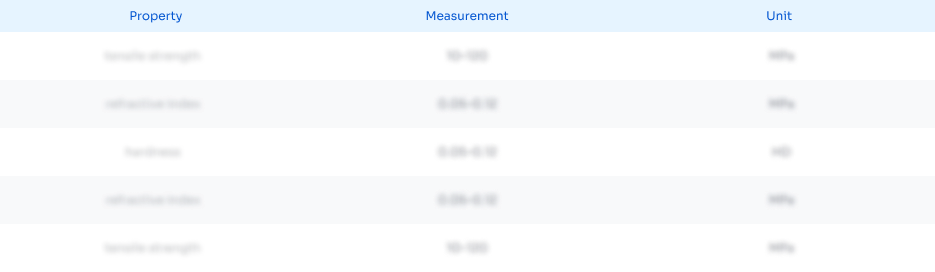
Abstract
Description
Claims
Application Information

- R&D Engineer
- R&D Manager
- IP Professional
- Industry Leading Data Capabilities
- Powerful AI technology
- Patent DNA Extraction
Browse by: Latest US Patents, China's latest patents, Technical Efficacy Thesaurus, Application Domain, Technology Topic.
© 2024 PatSnap. All rights reserved.Legal|Privacy policy|Modern Slavery Act Transparency Statement|Sitemap