Workpiece welding seam polishing method, terminal equipment and polishing control assembly
A technology for controlling components and terminal equipment. It is applied in metal processing equipment, grinding/polishing equipment, automatic grinding control devices, etc. It can solve the problems of poor grinding effect and low efficiency of grinding plan, and improve grinding efficiency and grinding track. Smooth, adaptive effects
- Summary
- Abstract
- Description
- Claims
- Application Information
AI Technical Summary
Problems solved by technology
Method used
Image
Examples
Embodiment 1
[0053] The following introduces Embodiment 1 of the workpiece weld grinding method applied to terminal equipment provided by the present application, see figure 1 , embodiment one includes:
[0054] S11. Obtain the coordinate data of the starting and ending points of the workpiece weld from the grinding control component;
[0055] S12. Using a mathematical software platform to generate a grinding trajectory according to the coordinate data;
[0056] S13. Send the grinding trajectory to the grinding control component, so that the grinding control component controls the industrial robot to grind the weld seam of the workpiece according to the grinding trajectory.
[0057] In the process of grinding workpiece welds, two ends are mainly involved, one end is the grinding control component, which is used to realize the data collection of workpiece welds, such as collecting the coordinate data of the starting and ending points of workpiece welds, and sending them to the terminal equ...
Embodiment 2
[0069] see Figure 4 , embodiment two specifically includes:
[0070] S41. Obtain the coordinate data of the starting and ending points of the workpiece weld from the grinding control component, and input it into the matlab platform.
[0071] S42. Determine the inclination angle of the workpiece weld according to the coordinate data of the starting and ending points of the workpiece weld on the XY plane.
[0072] S43. According to the inclination angle, the actual running radius, angular velocity and speed during the grinding process, calculate the track point data of the workpiece weld on the XY plane; use the X-axis compensation value and the Y-axis compensation value to correct the track point data ;
[0073] S44. Generate a grinding trajectory on the XY plane according to the trajectory point data and the initial grinding point data on the XY plane, wherein the initial grinding point data on the XY plane is equal to the coordinate data of the starting point of the workpi...
PUM
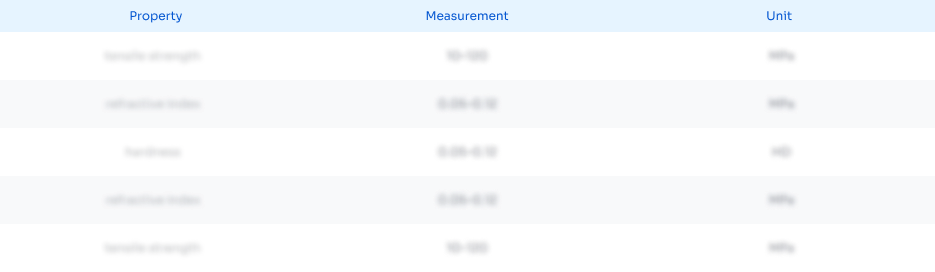
Abstract
Description
Claims
Application Information

- R&D Engineer
- R&D Manager
- IP Professional
- Industry Leading Data Capabilities
- Powerful AI technology
- Patent DNA Extraction
Browse by: Latest US Patents, China's latest patents, Technical Efficacy Thesaurus, Application Domain, Technology Topic, Popular Technical Reports.
© 2024 PatSnap. All rights reserved.Legal|Privacy policy|Modern Slavery Act Transparency Statement|Sitemap|About US| Contact US: help@patsnap.com