Method for welding thin plates with thick plates
A welding method and thin plate technology, applied in welding equipment, auxiliary welding equipment, welding/cutting auxiliary equipment, etc., can solve the problems of difficulty in guaranteeing the quality of the weld, large overall deformation of the product, and inability to guarantee the accuracy, and achieve the quality of the weld. Easy to guarantee and guarantee the effect of precision
- Summary
- Abstract
- Description
- Claims
- Application Information
AI Technical Summary
Problems solved by technology
Method used
Image
Examples
Embodiment Construction
[0028] The following will clearly and completely describe the technical solutions in the embodiments of the present invention with reference to the accompanying drawings in the embodiments of the present invention. Obviously, the described embodiments are only some, not all, embodiments of the present invention. Based on the embodiments of the present invention, all other embodiments obtained by persons of ordinary skill in the art without making creative efforts belong to the protection scope of the present invention.
[0029] see Figure 1-4 , the present invention provides a technical solution: a welding method for a thin plate and a thick plate, comprising the following steps:
[0030] Step S1: Prepare the thin and thick plates to be welded, and fix the positions of the thin and thick plates to be welded, and the preparatory work is completed;
[0031] Step S2: flanging the position of the thin plate to be welded, the flanging distance is 2-4 times of the thin plate, the ...
PUM
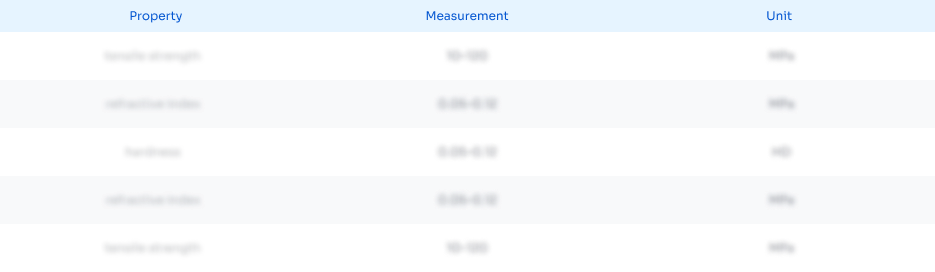
Abstract
Description
Claims
Application Information

- Generate Ideas
- Intellectual Property
- Life Sciences
- Materials
- Tech Scout
- Unparalleled Data Quality
- Higher Quality Content
- 60% Fewer Hallucinations
Browse by: Latest US Patents, China's latest patents, Technical Efficacy Thesaurus, Application Domain, Technology Topic, Popular Technical Reports.
© 2025 PatSnap. All rights reserved.Legal|Privacy policy|Modern Slavery Act Transparency Statement|Sitemap|About US| Contact US: help@patsnap.com