System and method for rapid replacement and clamping based on zero point positioning
A zero-point positioning and fast technology, applied in positioning devices, manufacturing computing systems, transportation and packaging, etc., can solve the problems of not meeting the processing needs of small batches of multi-variety products, not involving human-computer interaction, and not having equipment transformation technology, etc. Achieve the effects of shortening the development cycle, reducing costs, and good application effects
- Summary
- Abstract
- Description
- Claims
- Application Information
AI Technical Summary
Problems solved by technology
Method used
Image
Examples
Embodiment Construction
[0040] In order to better understand the above technical solutions, the technical solutions of the present application will be described in detail below through the accompanying drawings and specific examples. It should be understood that the embodiments of the present application and the specific features in the examples are detailed descriptions of the technical solutions of the present application, and It is not a limitation to the technical solutions of the present application, and the embodiments of the present application and the technical features in the embodiments can be combined without conflict.
[0041] A quick change system based on zero point positioning provided by the embodiment of the present application will be further described in detail below in conjunction with the accompanying drawings. The specific implementation methods may include (such as Figure 1~4 Shown): robot, clamping platform, quick-change pallet 1, machining center, automatic gas path connectio...
PUM
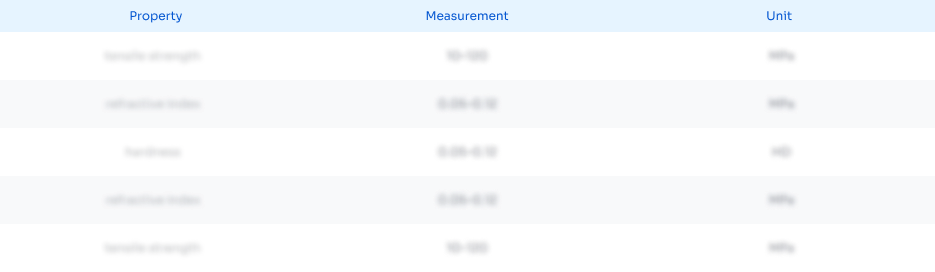
Abstract
Description
Claims
Application Information

- R&D
- Intellectual Property
- Life Sciences
- Materials
- Tech Scout
- Unparalleled Data Quality
- Higher Quality Content
- 60% Fewer Hallucinations
Browse by: Latest US Patents, China's latest patents, Technical Efficacy Thesaurus, Application Domain, Technology Topic, Popular Technical Reports.
© 2025 PatSnap. All rights reserved.Legal|Privacy policy|Modern Slavery Act Transparency Statement|Sitemap|About US| Contact US: help@patsnap.com