Parameterized control system and method for cooling gas jet in metal cutting
A cooling gas and control system technology, applied to controllers with specific characteristics, electric controllers, etc., can solve problems such as low efficiency, difficult parameterization and quantitative adjustment, and inability to cut the best cooling effect, so as to reduce the impact and realize Self-feedback adjustment, the effect of improving stability
- Summary
- Abstract
- Description
- Claims
- Application Information
AI Technical Summary
Problems solved by technology
Method used
Image
Examples
Embodiment Construction
[0049] In this example, if figure 1 As shown, a parameterized control system for cooling gas jets in metal cutting, including: computer PID control system, electric slide 1, constant pressure valve 2, mass flow controller 3, nozzle 4, infrared temperature sensor 5. Adjustable nozzle bracket 6 and adjustable infrared temperature sensor bracket 7;
[0050] On the upper table 1-1 of the electric sliding table 1, the constant pressure valve 2 and the mass flow controller 3 are respectively fixed by bolts; the infrared temperature sensor 5 and the nozzle 4 are respectively fixed on the adjustable infrared temperature sensor bracket 7 and the adjustable type nozzle holder 6; such as figure 2 As shown, the adjustable nozzle bracket 6 is provided with a U-shaped nozzle bracket 9 on the fixed end 10 of the nozzle bracket, wherein the U-shaped nozzle bracket 9 can adjust the relative angle relative to the fixed end 10 of the nozzle bracket. The middle of 9 is rotationally connected w...
PUM
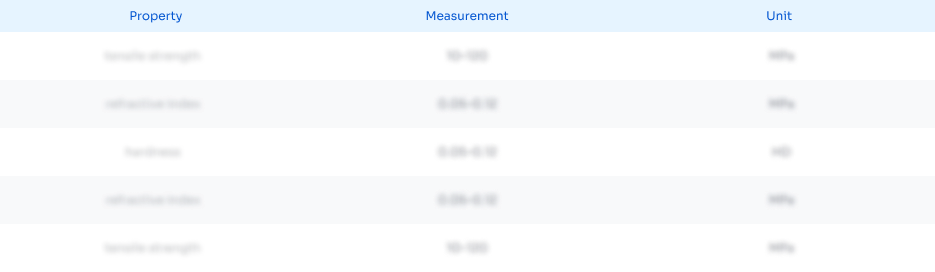
Abstract
Description
Claims
Application Information

- Generate Ideas
- Intellectual Property
- Life Sciences
- Materials
- Tech Scout
- Unparalleled Data Quality
- Higher Quality Content
- 60% Fewer Hallucinations
Browse by: Latest US Patents, China's latest patents, Technical Efficacy Thesaurus, Application Domain, Technology Topic, Popular Technical Reports.
© 2025 PatSnap. All rights reserved.Legal|Privacy policy|Modern Slavery Act Transparency Statement|Sitemap|About US| Contact US: help@patsnap.com