Multi-mode combined power cycle system based on transcritical CO2 and method
A combined power and circulation system technology, applied in the cooling of machines/engines, turbines/propulsion devices, engine components, etc., can solve the problems that the engine cannot further increase the Mach number, the structure of the pre-cooling system is large and complex, and the pre-cooling capacity is insufficient , to maximize energy utilization, reduce structural complexity, and facilitate portability and storage
- Summary
- Abstract
- Description
- Claims
- Application Information
AI Technical Summary
Problems solved by technology
Method used
Image
Examples
Embodiment Construction
[0014] Refer below figure 1 Describe the operation process of the multi-mode combined power cycle system based on transcritical CO2.
[0015] figure 1 It is a multi-mode combined power cycle system based on transcritical CO2 proposed by the present invention. The working process of the system is as follows: It can be divided into 3 modes (low speed mode, high speed mode and super high speed mode).
[0016] Turbine mode: the flight Mach number is 0~0.9; the first switch 11 and the second switch 16 are closed, and the outer duct 3 is opened by regulating the intake duct 1, and the air enters the intake duct 1 and is divided into the inner duct 2 And in the outer duct 3, the air in the outer duct 3 directly enters the main combustion chamber 6, the air in the inner duct 2 enters the compressor 5 for boosting, and the high-pressure air enters the main combustion chamber 6 for combustion, high temperature and high pressure The air passes through the air turbine 7 to perform work...
PUM
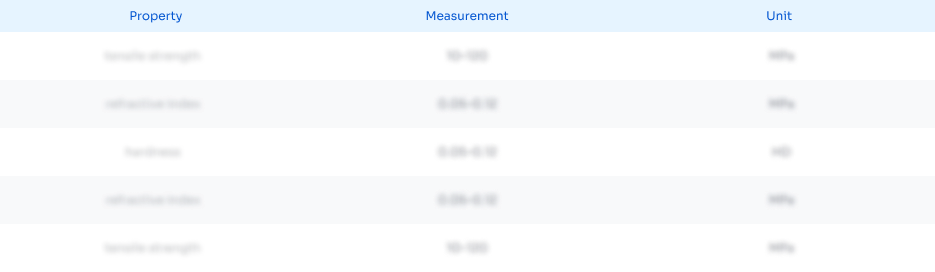
Abstract
Description
Claims
Application Information

- R&D
- Intellectual Property
- Life Sciences
- Materials
- Tech Scout
- Unparalleled Data Quality
- Higher Quality Content
- 60% Fewer Hallucinations
Browse by: Latest US Patents, China's latest patents, Technical Efficacy Thesaurus, Application Domain, Technology Topic, Popular Technical Reports.
© 2025 PatSnap. All rights reserved.Legal|Privacy policy|Modern Slavery Act Transparency Statement|Sitemap|About US| Contact US: help@patsnap.com