Preparation method of insulating paper board
A technology for insulating cardboard and cardboard, applied in the direction of machining/deformation, etc., can solve the problems of uneven density, easy existence of holes and water channels in the final product, uneven thickness, etc.
- Summary
- Abstract
- Description
- Claims
- Application Information
AI Technical Summary
Problems solved by technology
Method used
Image
Examples
Embodiment 1
[0028] Embodiment one: The manufacture method of prior art (containing binder) 50mm cardboard:
[0029] 1. Cutting of the finished veneer: Take 17 sheets of 3mm cardboard, and cut the cardboard according to the size of the required product.
[0030] 2. Pad spacer stays: place spacer stays between the cardboards, and place different numbers of stays between each adjacent cardboard. The number of stays is determined according to the size of the finished product, and the distance between the stays does not exceed 300mm.
[0031] 3. Cardboard drying: Put the cardboard with the stays into the hot air circulation drying oven, dry at 125°C, and the drying time is more than 36 hours, subject to the final cardboard moisture being less than 1%.
[0032] 4. Cardboard cooling: Run the dried cardboard to the glue coating area, and use a fan to cool down. The cooling time is about 2 hours.
[0033] 5. Glue application: Use a glue applicator to apply glue to the cardboard, and stack the c...
Embodiment 2
[0036] Embodiment two: 10mm cardboard production of the present invention:
[0037] 1. Take wet cardboard: Take the wet cardboard corresponding to the finished product 10mm in thickness of about 36mm, and the quantity is 1 piece.
[0038] 2. Wet cardboard humidification and stacking: add water to the surface of the wet cardboard until the water surface evenly covers the cardboard surface, and use plastic rollers to roll.
[0039] 3. Stand still: put the stacked cardboards for 6 hours to make the moisture of the wet cardboards more uniform.
[0040] 4. Mold on wet cardboard: Place the wet cardboard on the mold with stainless steel mesh.
[0041] 5. Wet cardboard pressing:
[0042] ① Pre-pressing: Start the pressing button, manual control, the initial set pressure is 1Mpa, gradually increase the pressure, a single increase of 0.2Mpa, with the continuous loss of moisture in the wet cardboard, the pressure will gradually decrease, until the pressure drops to the last set press...
Embodiment 3
[0045] Embodiment three: 15mm cardboard production:
[0046] 1. Take wet cardboard: take wet cardboard with a thickness of 27mm wet cardboard, and the quantity is 2 pieces.
[0047] 2. Wet cardboard humidification, stacking: Add water to the surface of the first cardboard until the water evenly covers the surface of the cardboard, and use a plastic roller to roll the surface of the second layer of cardboard in the same way as the first cardboard, and then Place the bottom surface of the second cardboard with the top surface of the first cardboard, edge-aligned and stacked.
[0048] 3. Stand still: put the stacked cardboards for 6 hours to make the moisture of the wet cardboards more uniform.
[0049] 4. Mold on wet cardboard: Place the wet cardboard on the mold with stainless steel mesh.
[0050] 5. Wet cardboard pressing:
[0051] ① Pre-pressing: Start the pressing button, manual control, the initial set pressure is 1Mpa, gradually increase the pressure, a single increas...
PUM
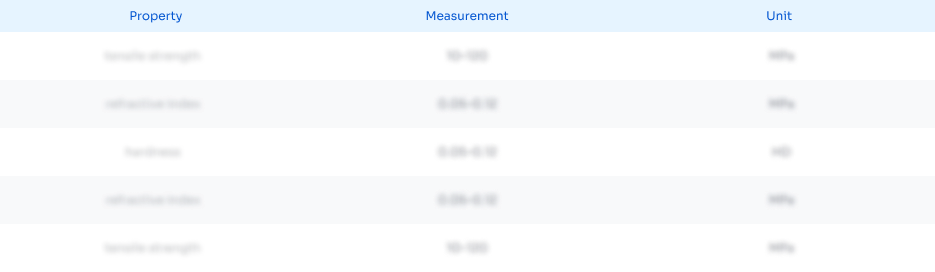
Abstract
Description
Claims
Application Information

- R&D
- Intellectual Property
- Life Sciences
- Materials
- Tech Scout
- Unparalleled Data Quality
- Higher Quality Content
- 60% Fewer Hallucinations
Browse by: Latest US Patents, China's latest patents, Technical Efficacy Thesaurus, Application Domain, Technology Topic, Popular Technical Reports.
© 2025 PatSnap. All rights reserved.Legal|Privacy policy|Modern Slavery Act Transparency Statement|Sitemap|About US| Contact US: help@patsnap.com