Fiber-based adsorption material and preparation method thereof and application of fiber-based adsorption material in palladium recovery
An adsorption material and fiber-based technology, applied in the field of fiber-based adsorption materials and their preparation, can solve the problems of poor practical applicability, reduced reactivity, and poor practicability, and achieve efficient adsorption and recovery, high adsorption efficiency, and practicality strong effect
- Summary
- Abstract
- Description
- Claims
- Application Information
AI Technical Summary
Problems solved by technology
Method used
Image
Examples
Embodiment 1
[0025] According to method A, 10g of polyacrylonitrile fiber was immersed in 180mL of diethylenetriamine solution, heated and stirred at 130°C under reflux for 5 hours, and the obtained product was washed until neutral. Submerge the washed product (fiber) in absolute ethanol, add 20 g of bromoacetic acid and adjust the pH of the solution to 10 with sodium hydroxide, reflux at 80° C. for 10 hours, and the obtained product is a modified polyacrylonitrile fiber. The modified polyacrylonitrile fibers were immersed in a mixed solvent composed of 50 mL of water and 50 mL of DMF, and activated by adding 0.008 mol of EDC and 0.008 mol of NHS at 30° C. for 1 hour. Disperse 2.36g of zirconium chloride and 2.55g of 2-aminoterephthalic acid in a mixed solvent composed of 90mL of water and 90mL of N'N-dimethylformamide, add activated modified polyacrylonitrile fibers, and heat at 120°C Reflux for 24 hours, filter and soak with ethanol, and the resulting solid was vacuum-dried at 60°C for 1...
Embodiment 2
[0027] The operation steps are the same as those in Example 1, the difference being that 4.05g of chromium nitrate (nonahydrate) is used as the metal salt to replace zirconium chloride when preparing the fiber-based adsorbent material, and the fiber-based adsorbent material is marked as PAN-MOF2.
Embodiment 3
[0029] According to method B, add 2.36g of zirconium chloride and 2.55g of 2-aminoterephthalic acid into 200mL of DMF in sequence, disperse ultrasonically for 20 minutes, and keep it airtight at 120°C for 20 hours. After cooling to room temperature, use ethanol to centrifuge. Vacuum dry at 70°C for 12 hours to obtain solid powder; 10g of polyacrylonitrile fiber was immersed in 180mL of diethylenetriamine, heated, stirred and refluxed at 130°C for 5 hours, and the obtained product was washed until neutral. Submerge the washed product (fiber) in absolute ethanol solvent, add 20 g of chloroacetic acid and adjust the pH of the solution to 10 with sodium hydroxide, reflux at 80° C. for 10 hours, and the obtained product is modified polyacrylonitrile fiber. Immerse the modified polyacrylonitrile fiber in a mixed solvent composed of 90mL water and 90mL DMF, add 0.008mol EDC·HCl and 0.008mol NHS, stir and activate at 30°C for 1 hour, add solid powder, and reflux at 70°C for 20 hours ,...
PUM
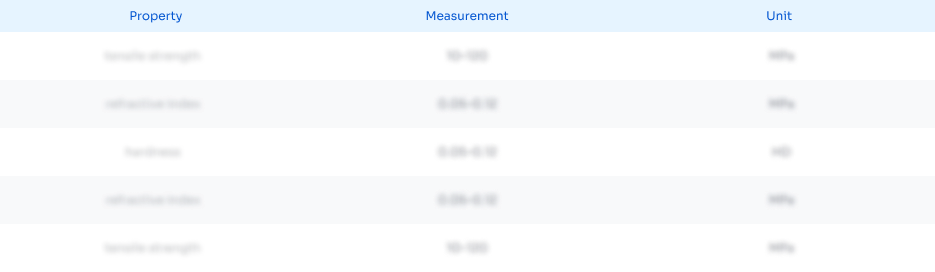
Abstract
Description
Claims
Application Information

- R&D
- Intellectual Property
- Life Sciences
- Materials
- Tech Scout
- Unparalleled Data Quality
- Higher Quality Content
- 60% Fewer Hallucinations
Browse by: Latest US Patents, China's latest patents, Technical Efficacy Thesaurus, Application Domain, Technology Topic, Popular Technical Reports.
© 2025 PatSnap. All rights reserved.Legal|Privacy policy|Modern Slavery Act Transparency Statement|Sitemap|About US| Contact US: help@patsnap.com