Additive and subtractive composite manufacturing part deformation prediction and control method and equipment
A control method and technology of adding and subtracting materials, applied in computer-aided design, design optimization/simulation, special data processing applications, etc., can solve the problems of simulation parts not being too large, long calculation time, large calculation amount, etc., to reduce heat The effect of deformation amount, speed up calculation, and simplification of calculation process
- Summary
- Abstract
- Description
- Claims
- Application Information
AI Technical Summary
Problems solved by technology
Method used
Image
Examples
Embodiment Construction
[0049] The present invention will be further described in detail below in conjunction with the accompanying drawings and embodiments.
[0050] see figure 1 The coaxial powder-feeding laser melting additive manufacturing equipment includes an inert gas protection glove box 1, a laser cladding head 2 for spraying a laser beam 3 and metal powder 4, a substrate 6 for placing a component 5, and a heat-conducting silica gel 7 arranged under the substrate 6 and Heat conduction copper plate 8, heating liquid conduit 9, workbench 10, laser 11, optical fiber 12, powder feeder 13, powder feed barrel 14, powder feed pipe 15.
[0051] see figure 2 , a method for predicting and controlling the deformation of additive and subtractive composite manufacturing parts, comprising the following steps:
[0052] Step S1: Perform the following steps on the parts to be predicted image 3 The feature recognition shown is to extract the main features of the parts, decompose the features of the parts...
PUM
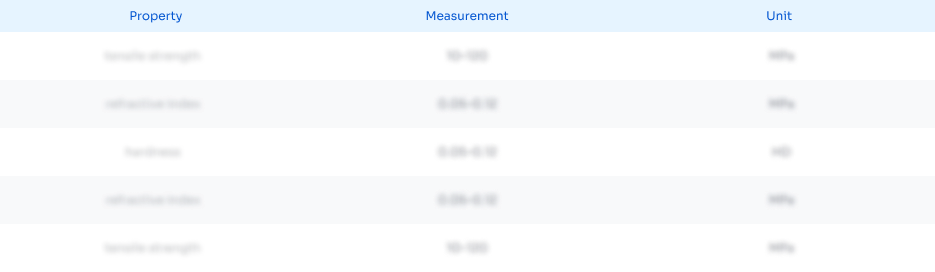
Abstract
Description
Claims
Application Information

- R&D
- Intellectual Property
- Life Sciences
- Materials
- Tech Scout
- Unparalleled Data Quality
- Higher Quality Content
- 60% Fewer Hallucinations
Browse by: Latest US Patents, China's latest patents, Technical Efficacy Thesaurus, Application Domain, Technology Topic, Popular Technical Reports.
© 2025 PatSnap. All rights reserved.Legal|Privacy policy|Modern Slavery Act Transparency Statement|Sitemap|About US| Contact US: help@patsnap.com