Uniform self-controlled gear heat treatment device and method based on asynchronous dual-frequency induction heating
A dual-frequency induction and self-control technology, used in heat treatment furnaces, heat treatment equipment, heat treatment process control and other directions, can solve the problems of expensive induction power supply, rough heating control method, poor heat treatment economy of gears, etc. Economical, improved uniformity effect
- Summary
- Abstract
- Description
- Claims
- Application Information
AI Technical Summary
Problems solved by technology
Method used
Image
Examples
Embodiment Construction
[0030] The present invention will be further described in detail below with reference to the accompanying drawings and specific embodiments.
[0031] like Figures 1 to 3As shown in the figure, a uniform self-control gear heat treatment device based on asynchronous dual-frequency induction heating includes a power box 1, an induction coil 2, a bracket 3, a gear height adjustment motor 4, a lead screw 5, a nut slider 6, and a slider guide column. 7. Infrared temperature measuring camera 8 and computer; the gear height adjustment motor 4 is vertically fixed on the bottom of the bracket 3, the motor shaft of the gear height adjustment motor 4 faces upwards, the lead screw 5 is vertically arranged, and the lead screw 5 is at the bottom The end is fixed coaxially with the motor shaft of the gear height-adjusting motor 4 through a coupling; the slider guide column 7 adopts a parallel double-column structure, and the slider guide column 7 is vertically fixed on the side of the gear h...
PUM
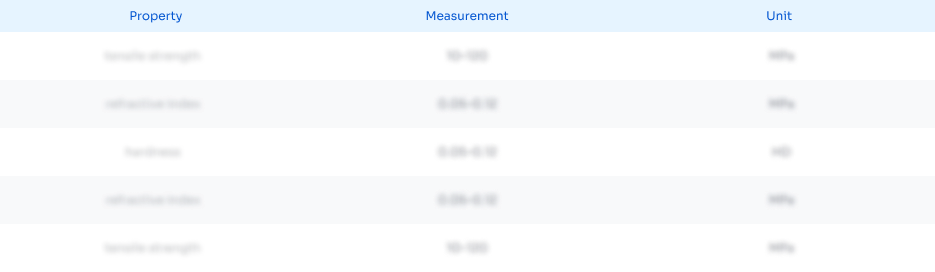
Abstract
Description
Claims
Application Information

- R&D
- Intellectual Property
- Life Sciences
- Materials
- Tech Scout
- Unparalleled Data Quality
- Higher Quality Content
- 60% Fewer Hallucinations
Browse by: Latest US Patents, China's latest patents, Technical Efficacy Thesaurus, Application Domain, Technology Topic, Popular Technical Reports.
© 2025 PatSnap. All rights reserved.Legal|Privacy policy|Modern Slavery Act Transparency Statement|Sitemap|About US| Contact US: help@patsnap.com