A Method for Evaluation of Robot End Stiffness Performance
An evaluation method and robot technology, applied in the field of robots, can solve the problems such as the inability to timely reflect the stiffness performance of the robot end, the high cost of joint stiffness testing, and the complex evaluation method, and achieve the effect of simple evaluation method, easy operation, and improved accuracy.
- Summary
- Abstract
- Description
- Claims
- Application Information
AI Technical Summary
Problems solved by technology
Method used
Image
Examples
Embodiment Construction
[0085] The industrial computer and the robot controller are connected through Ethernet / IP data, the six-dimensional force sensor is connected through TCP / IP data, and the laser displacement sensor is connected through USB data; the robot joint stiffness matrix is obtained, the robot Jacobian matrix is solved, and the end robot stiffness is established Ellipsoid, the intersection of stiffness ellipsoid surface and end force vector and the product of the distance from the center of the ellipsoid and the length of the force vector are used as the evaluation index of the robot end stiffness.
[0086] The material of the connecting piece and the connecting flange in the device of the present invention is 45 steel, the elastic modulus is 196-206 Gpa, the Young's modulus is 79 Gpa, and the Poisson's ratio is 0.3.
[0087] Attached to the following Figure 1-4 The present invention is further described in detail:
[0088] like figure 1 Shown is a flow chart of the robot tip stif...
PUM
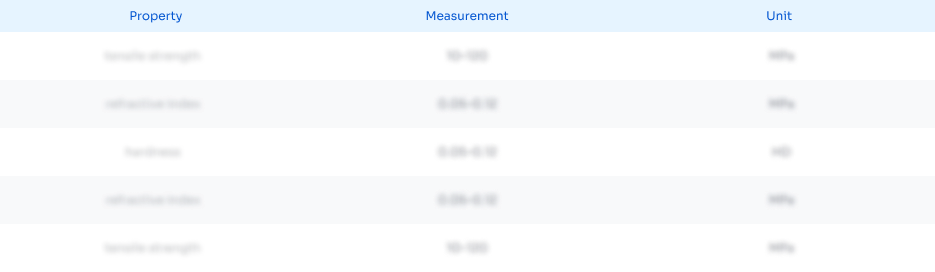
Abstract
Description
Claims
Application Information

- R&D
- Intellectual Property
- Life Sciences
- Materials
- Tech Scout
- Unparalleled Data Quality
- Higher Quality Content
- 60% Fewer Hallucinations
Browse by: Latest US Patents, China's latest patents, Technical Efficacy Thesaurus, Application Domain, Technology Topic, Popular Technical Reports.
© 2025 PatSnap. All rights reserved.Legal|Privacy policy|Modern Slavery Act Transparency Statement|Sitemap|About US| Contact US: help@patsnap.com