Steam turbine unit mounting technology
An installation process and technology for steam turbine units, applied in the field of steam turbines, can solve the problems of frequent maintenance and difficult control of installation process quality, and achieve the effects of strong continuity, avoiding the risk of midway downtime and reducing rework.
- Summary
- Abstract
- Description
- Claims
- Application Information
AI Technical Summary
Problems solved by technology
Method used
Image
Examples
Embodiment 1
[0060] A steam turbine installation process, comprising the steps of:
[0061] S1. Process preparation: check that the strength and precision of the equipment meet the installation requirements of the unit, and the foundation surface is required to be flat and free of defects such as cracks, holes, honeycombs, pitted surfaces, and exposed ribs;
[0062] S2. Arrangement of parallel irons: Lay out the line according to the layout of the parallel irons, draw the position of the parallel irons, polish the position of the parallel irons, chisel the concrete surface where the parallel irons are installed to make the four corners of the parallel irons flat, and use the joint surface between the parallel irons and the concrete The coloring method checks to make the contact uniform, and the installation of pad iron requires uniform force everywhere;
[0063] The use of inclined pads must be paired, and the inclined plane must be corrected to ensure that the contact of the inclined plan...
Embodiment 2
[0087] On the basis of Example 1, when the generator bearing seat is installed, clean the insulating backing plate, and there must be no oil, sundries and other factors that affect the insulation. The insulation level is measured with a 1000V megohmmeter, and the resistance value must not be less than 1MΩ. Use a level to measure the elevation of the midsection, which should be the same as the elevation of the midsection of the steam turbine, and the levelness of the base should also be controlled within 0.20mm. The center position deviation is not greater than 2mm, and the axial position is measured by the center of the rear bearing of the steam turbine.
Embodiment 3
[0089] On the basis of Example 1, the measured values of bearing pad tightening force, bearing pad top clearance, shaft seal clearance and bearing pad side clearance should meet the following requirements:
[0090]
[0091] The above units are mm.
PUM
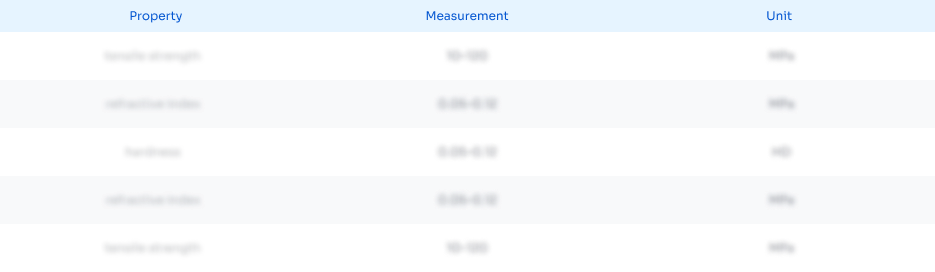
Abstract
Description
Claims
Application Information

- R&D
- Intellectual Property
- Life Sciences
- Materials
- Tech Scout
- Unparalleled Data Quality
- Higher Quality Content
- 60% Fewer Hallucinations
Browse by: Latest US Patents, China's latest patents, Technical Efficacy Thesaurus, Application Domain, Technology Topic, Popular Technical Reports.
© 2025 PatSnap. All rights reserved.Legal|Privacy policy|Modern Slavery Act Transparency Statement|Sitemap|About US| Contact US: help@patsnap.com