Online prediction method for stagnation point heat flow in flight process of aircraft
A flight process and aircraft technology, applied in the direction of instruments, electrical digital data processing, computer-aided design, etc., can solve problems such as limited heat flow function forms, and achieve the effect of accurate heat flow prediction
- Summary
- Abstract
- Description
- Claims
- Application Information
AI Technical Summary
Problems solved by technology
Method used
Image
Examples
Embodiment Construction
[0024] The present invention will be further elaborated below.
[0025] Firstly, the hypersonic hemispherical head flows around, under the dissociated gas thermal equilibrium flow, the zero angle of attack stagnation point steady continuous laminar flow, the engineering estimation formula of the steady state heat transfer heat flow rate:
[0026]
[0027] where q s is the heat flow rate at the stagnation point; ρ ∞ is the flow density; R N is the radius of curvature of the spherical head; hw is the wall enthalpy; stagnation enthalpy hs is,
[0028]
[0029] where V ∞ is the flow velocity; T ∞ is the flow temperature.
[0030] According to this formula, and considering the flight conditions given in this topic, the heat flow formula is simplified to the following form:
[0031]
[0032] Among them, A, B, C, and D are coefficients to be fitted, and logarithms are taken on both sides:
[0033] lnq s =-0.5 lnR N +lnA+B·lnρ ∞ +C lnV ∞ +D·ln(T W -T ∞ ) (4)
[...
PUM
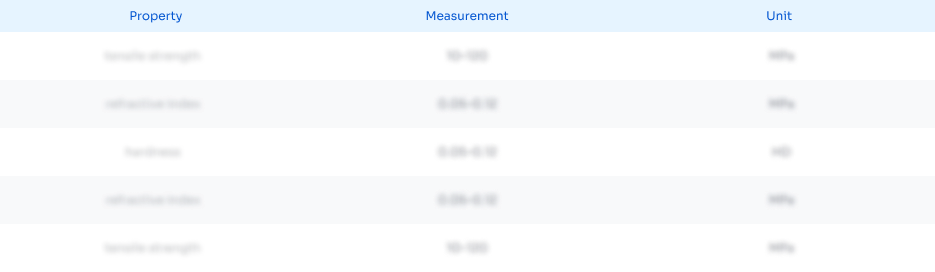
Abstract
Description
Claims
Application Information

- R&D
- Intellectual Property
- Life Sciences
- Materials
- Tech Scout
- Unparalleled Data Quality
- Higher Quality Content
- 60% Fewer Hallucinations
Browse by: Latest US Patents, China's latest patents, Technical Efficacy Thesaurus, Application Domain, Technology Topic, Popular Technical Reports.
© 2025 PatSnap. All rights reserved.Legal|Privacy policy|Modern Slavery Act Transparency Statement|Sitemap|About US| Contact US: help@patsnap.com