Rubber-covered wire optical cable easy to strip
A technology for a sheathed optical cable and an optical fiber unit, which is applied in the field of easy-to-peel sheathed optical cables, can solve the problems of large bonding force, inconvenient connection operation, and difficult peeling of the sheath, and achieves convenient connection operation, improved stripping performance, and improved strippability. Effect
- Summary
- Abstract
- Description
- Claims
- Application Information
AI Technical Summary
Problems solved by technology
Method used
Image
Examples
Embodiment 1
[0021] The structure of embodiment 1 is as figure 1 As shown, it includes a sheath 3 with a rectangular cross-section, and an optical fiber unit 1 is coated in the middle of the sheath. The optical fiber unit is a single-core optical fiber, and the number of cores can be 1 core. The corresponding optical fiber units on both sides of the sheath A reinforcing member is installed symmetrically, the reinforcing member is GRP, and a groove shrinking from the outside to the inside is arranged symmetrically in the upper and lower middle of the sheath corresponding to the optical fiber unit. , that is, the top is square and the lower part is V-shaped. The V-shaped bottom of the groove reaches or approaches the optical fiber unit to form a deep groove. The distance between the apex of the V-shaped bottom of the deep groove and the surface of the optical fiber unit is 0.1 ~0.2mm. The described deep groove is filled with a separation filling layer 4, and the resin material of the separa...
Embodiment 2
[0023] The structure of embodiment 2 is as figure 2 As shown, the difference between its structure and Embodiment 1 is that the deep groove is V-shaped in the transverse section of the sheath, the optical fiber unit is a single-core optical fiber, and the number of cores can be 2 cores, so The reinforcements described above are steel wires, and the rest of the structures are the same. The resin material of the separation filling layer is different from the resin material of the sheath, wherein the resin material of the sheath has a solubility parameter of 18.1 (J / cm 3 ) 0 . 5 The flame-retardant LSZH, the resin material of the separation filling layer has a solubility parameter of 20.1 (J / cm 3 ) 0 . 5 Polyacrylate flame retardant resin, polyacrylate flame retardant resin components and content by weight: polyacrylic acid 50%, ATH44%, organic expanded nano-soil 2%, antioxidant 1%, anti-UV agent 2%, White toner 1%.
[0024] The manufacturing process of the present embo...
Embodiment 3
[0025] The structure of embodiment 3 is as image 3 As shown, the difference between its structure and embodiment 1 is that the steel wire sling 5 is connected by a connecting belt on one side of the sheath, the steel wire sling includes a steel wire and an outer sheath, and the outer sheath is integrated with the connecting sling and the sheath. All the other structures are the same as in Example 1. The resin material of the separation filling layer is different from the resin material of the sheath, wherein the resin material of the sheath has a solubility parameter of 19.2 (J / cm 3 ) 0 . 5 Flame-retardant PVC, the resin material of the separation filling layer has a solubility parameter of 17.5 (J / cm 3 ) 0 . 5 The polyethylene flame retardant resin, polyethylene flame retardant resin components and content by weight are: polyethylene 44%, MTH 50%, organic expanded nano-soil 2%, antioxidant 1%, anti-UV agent 3%.
[0026] The production process of this embodiment is as...
PUM
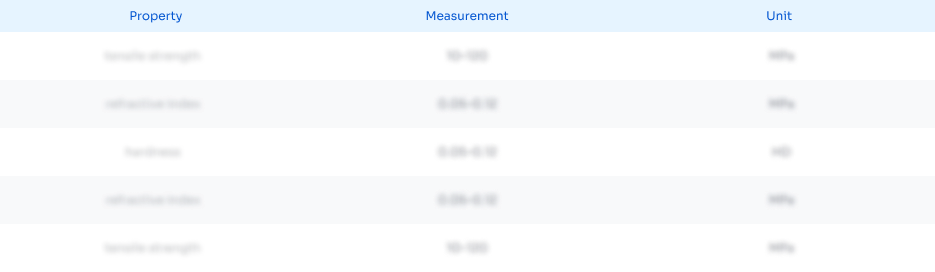
Abstract
Description
Claims
Application Information

- R&D
- Intellectual Property
- Life Sciences
- Materials
- Tech Scout
- Unparalleled Data Quality
- Higher Quality Content
- 60% Fewer Hallucinations
Browse by: Latest US Patents, China's latest patents, Technical Efficacy Thesaurus, Application Domain, Technology Topic, Popular Technical Reports.
© 2025 PatSnap. All rights reserved.Legal|Privacy policy|Modern Slavery Act Transparency Statement|Sitemap|About US| Contact US: help@patsnap.com