Method for comprehensively recovering various valuable metals in copper slag floating copper tailings
A technology for valuable metals and copper tailings, applied in chemical instruments and methods, flotation, process efficiency improvement, etc., can solve problems such as inability to utilize copper slag resources, single type of valuable metals, waste of resources, etc., to achieve The effects of avoiding excessive deposition of soot, improving resource utilization, and reducing energy consumption
- Summary
- Abstract
- Description
- Claims
- Application Information
AI Technical Summary
Problems solved by technology
Method used
Image
Examples
Embodiment 1
[0059] Such as figure 1 , 2 As shown, a kind of comprehensive recovery method of multiple valuable metals in copper slag floating copper tailings of the present embodiment comprises the following steps:
[0060] Step 1. Direct Restore
[0061] The composite additive of calcium oxide and sodium carbonate (GaO:Na 2 CO 3 = 2) Mix 10% of the column with copper slag evenly and put it into a tube furnace, and feed a gas mixture of methane, hydrogen and argon for reduction roasting. The roasting temperature is 700°C, and the roasting time is 120min. The constant volume fraction of dry argon is 50%, the concentrations of methane and hydrogen used are selected as 5vol% and 45vol%, and the total flow rate of the mixed gas into the tube furnace is 800mL / min to remove zinc and lead in the slag and other harmful impurities, and zinc and lead are recovered, and the lead-zinc grade of the dust obtained is above 30%, which can be used as raw materials for lead-zinc smelting;
[0062] Ste...
Embodiment 2
[0067] Such as figure 1 , 2 As shown, a kind of comprehensive recovery method of multiple valuable metals in copper slag floating copper tailings of the present embodiment comprises the following steps:
[0068] Step 1. Direct Restore
[0069] The composite additive of calcium oxide and sodium carbonate (GaO:Na 2 CO 3 = 1.5) The ratio of 15% is mixed evenly with copper slag and put into the tube furnace, and the gas mixture of methane, hydrogen and argon is introduced to carry out reduction roasting, the roasting temperature is 800°C, the roasting time is 100min, the mixed gas The constant volume fraction of dry argon is 50%, the concentrations of methane and hydrogen used are selected as 10vol% and 40vol%, and the total flow rate of the mixed gas into the tube furnace is 800mL / min to remove zinc and lead in the slag and other harmful impurities, and zinc and lead are recovered, and the lead-zinc grade of the dust obtained is above 30%, which can be used as raw materials f...
Embodiment 3
[0075] Such as figure 1 , 2 As shown, a kind of comprehensive recovery method of multiple valuable metals in copper slag floating copper tailings of the present embodiment comprises the following steps:
[0076] Step 1. Direct Restore
[0077] The composite additive of calcium oxide and sodium carbonate (GaO:Na 2 CO 3 = 2) Mix the 15% proportion with copper slag evenly, put it into the tube furnace, and feed the gas mixture of methane, hydrogen and argon to carry out reduction roasting, the roasting temperature is 900°C, the roasting time is 90min, the mixed gas The constant volume fraction of dry argon is 50%, the concentrations of methane and hydrogen used are selected as 15vol% and 35vol%, and the total flow rate of the mixed gas into the tube furnace is 700mL / min to remove zinc and lead in the slag and other harmful impurities, and zinc and lead are recovered, and the lead-zinc grade of the dust obtained is above 30%, which can be used as raw materials for lead-zinc sm...
PUM
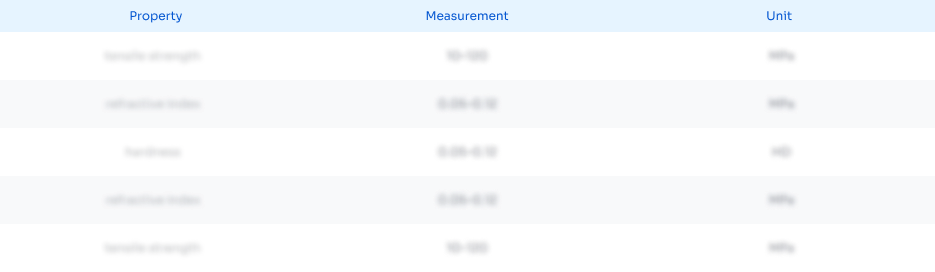
Abstract
Description
Claims
Application Information

- R&D
- Intellectual Property
- Life Sciences
- Materials
- Tech Scout
- Unparalleled Data Quality
- Higher Quality Content
- 60% Fewer Hallucinations
Browse by: Latest US Patents, China's latest patents, Technical Efficacy Thesaurus, Application Domain, Technology Topic, Popular Technical Reports.
© 2025 PatSnap. All rights reserved.Legal|Privacy policy|Modern Slavery Act Transparency Statement|Sitemap|About US| Contact US: help@patsnap.com