Multi-point measurement pneumatic probe based on virtual hole row and application thereof
A multi-point measurement and probe technology, applied in the field of multi-point measurement pneumatic probes based on virtual hole rows, can solve the problem of increased flow field obstruction and disturbance, limited air source capacity, and improve the design of multi-hole pneumatic probes. Problems such as processing difficulty, to achieve the effect of small aerodynamic resistance and flow field disturbance, and low design and processing costs
- Summary
- Abstract
- Description
- Claims
- Application Information
AI Technical Summary
Problems solved by technology
Method used
Image
Examples
Embodiment 1
[0036] The multi-point measurement aerodynamic probe based on the virtual hole row in this embodiment is proposed to meet the measurement requirements of the aerodynamic parameters of the cascade outlet section of the impulsive planar cascade wind tunnel.
[0037] The internal structure of the multi-point measurement pneumatic probe based on the virtual hole row in this embodiment is complicated, and it is difficult to realize the processing of the internal helix by the traditional processing method, and it needs to be processed and formed by additive manufacturing.
[0038] Such as figure 1 As shown, the multi-point measurement pneumatic probe based on the virtual hole row in this embodiment is composed of a measurement section 1 , a transition section 2 and a clamping section 3 connected in sequence. The probe body is integrally formed by stainless steel additive manufacturing. The measuring section 1 is a cylinder, and the surface roughness is reduced by sandblasting and p...
PUM
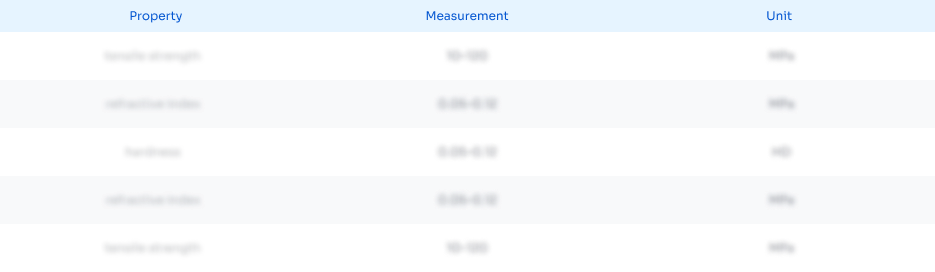
Abstract
Description
Claims
Application Information

- R&D
- Intellectual Property
- Life Sciences
- Materials
- Tech Scout
- Unparalleled Data Quality
- Higher Quality Content
- 60% Fewer Hallucinations
Browse by: Latest US Patents, China's latest patents, Technical Efficacy Thesaurus, Application Domain, Technology Topic, Popular Technical Reports.
© 2025 PatSnap. All rights reserved.Legal|Privacy policy|Modern Slavery Act Transparency Statement|Sitemap|About US| Contact US: help@patsnap.com