Samarium cobalt vacuum sintering furnace and application method thereof
A vacuum sintering furnace, samarium cobalt technology, applied in the furnace, charge, furnace type and other directions, can solve the problems of slow cooling rate, inability to volatilize, single cooling rate, etc., to improve cooling uniformity, improve cooling speed, and inhibit volatilization. Effect
- Summary
- Abstract
- Description
- Claims
- Application Information
AI Technical Summary
Problems solved by technology
Method used
Image
Examples
Embodiment 1
[0058] Step 1: Sintering
[0059] Put the prepared samarium-cobalt magnet green body into the vacuum sintering furnace described in the general embodiment, then close the furnace cover and vacuumize (vacuumize to 3×10 -3 Pa), at this stage the sintering protective cover remains open, the furnace body is heated, the samarium-cobalt magnet is heated to the pre-sintering temperature of 1185 °C through three stages of heat preservation and exhaust at 200°C, 500°C and 900°C, and the sintering protective cover is lowered to Fit closely with the rotating chassis, fill the furnace body with argon gas, the argon gas passes through the intake valve of the sintering protective cover to push up the differential pressure block, and then fills the argon gas into the sintering protective cover. This process is controlled by the pressure gauge and the program. Keep the vacuum at -0.05MPa and make it stable, then raise the temperature to 1200°C for 2 hours, then cool down to 1180°C and keep it...
Embodiment 2
[0064] Step 1: Sintering
[0065] Put the prepared samarium-cobalt magnet green body into the vacuum sintering furnace described in the general embodiment, then close the furnace cover and vacuumize (vacuumize to 3×10 -3 Pa), at this stage the sintering protective cover remains open, the furnace body is heated, the samarium-cobalt magnet is heated to the pre-sintering temperature of 1185 °C through three stages of heat preservation and exhaust at 200°C, 500°C and 900°C, and the sintering protective cover is lowered to Fit closely with the rotating chassis, fill the furnace body with argon gas, the argon gas passes through the intake valve of the sintering protective cover to push up the differential pressure block, and then fills the argon gas into the sintering protective cover. This process is controlled by the pressure gauge and the program. Keep the vacuum at -0.05MPa and make it stable, then raise the temperature to 1200°C for 2 hours, then cool down to 1180°C and keep it...
Embodiment 3
[0070] Put the prepared samarium-cobalt magnet green body into the vacuum sintering furnace described in the general embodiment, then close the furnace cover and vacuumize (vacuumize to 3×10 -3Pa), at this stage the sintering protective cover remains open, the furnace body is heated, the samarium-cobalt magnet is heated to the pre-sintering temperature of 1185 °C through three stages of heat preservation and exhaust at 200°C, 500°C and 900°C, and the sintering protective cover is lowered to Fit closely with the rotating chassis, fill the furnace body with argon gas, the argon gas passes through the intake valve of the sintering protective cover to push up the differential pressure block, and then fills the argon gas into the sintering protective cover. This process is controlled by the pressure gauge and the program. Keep the vacuum at -0.05MPa and make it stable, then raise the temperature to 1200°C for 2 hours, then cool down to 1180°C for 4 hours, then open the protective co...
PUM
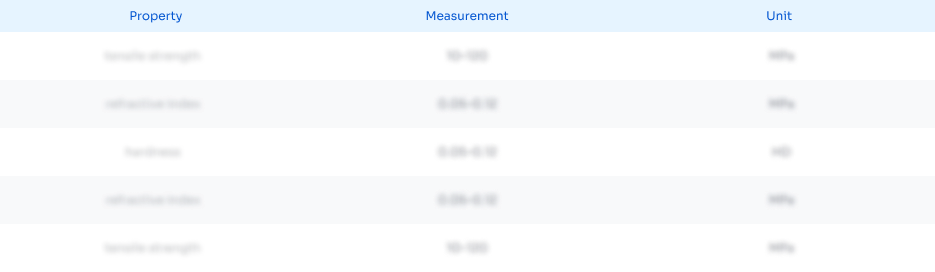
Abstract
Description
Claims
Application Information

- Generate Ideas
- Intellectual Property
- Life Sciences
- Materials
- Tech Scout
- Unparalleled Data Quality
- Higher Quality Content
- 60% Fewer Hallucinations
Browse by: Latest US Patents, China's latest patents, Technical Efficacy Thesaurus, Application Domain, Technology Topic, Popular Technical Reports.
© 2025 PatSnap. All rights reserved.Legal|Privacy policy|Modern Slavery Act Transparency Statement|Sitemap|About US| Contact US: help@patsnap.com