Color fixing agent and cotton cloth pad dyeing process using color fixing agent
A color-fixing agent and technology for cotton fabrics, applied in the field of pad dyeing and dyeing of cotton fabrics, can solve the problems of poor washability of fabrics and fabric fading, and achieve the effects of delaying fading, saving energy consumption and enhancing washability.
- Summary
- Abstract
- Description
- Claims
- Application Information
AI Technical Summary
Problems solved by technology
Method used
Image
Examples
preparation example 1-3
[0072] Color fixing agent is made by the following steps:
[0073] Step 1: Stir ammonium chloride and diethylenetriamine at a speed of 700r / min for 25min, heat up to 100°C, and keep warm for 1h to obtain mixture a;
[0074] Step 2: Add dicyandiamide and ethylene glycol to mixture A, raise the temperature to 130° C., and keep the temperature for 30 minutes to obtain mixture b;
[0075] Step 3: when the temperature of the mixture B is lowered to 90°C, add water and glacial acetic acid to obtain the mixture c;
[0076] Step 4: Add nano-chitin to the mixture C, and stir for 15 minutes at a rotating speed of 900 r / min to obtain a mixture d, which is the color fixing agent.
[0077] Wherein, the weight parts that dicyandiamide, ammonium chloride, diethylenetriamine, ethylene glycol, acetic acid, nano chitin and water add are as shown in table 1:
[0078] Table 1
[0079]
preparation example 4-6
[0081] The difference between Preparation Example 4-6 and Preparation Example 3 is that: in Step 4 of Preparation Example 4-6, sodium hydroxide, gelatin and carrageenan were added. The specific color fixing agent preparation process steps are as follows:
[0082] Step 1: Stir ammonium chloride and diethylenetriamine at a speed of 700r / min for 25min, heat up to 100°C, and keep warm for 1h to obtain mixture a;
[0083] Step 2: Add dicyandiamide and ethylene glycol to mixture A, raise the temperature to 130° C., and keep the temperature for 30 minutes to obtain mixture b;
[0084] Step 3: when the temperature of the mixture B is lowered to 90°C, add water and glacial acetic acid to obtain the mixture c;
[0085] Step 4: Add sodium hydroxide, nano-chitin, gelatin and carrageenan to mixture C, and stir for 15 minutes at a rotational speed of 900 r / min to obtain mixture d, which is the color fixing agent.
[0086] Wherein, the weight parts that sodium hydroxide, gelatin and carrag...
preparation example 7-9
[0090] The difference between Preparation Example 7-9 and Preparation Example 6 is that sodium caseinate is added in Step 4 of Preparation Example 7-9. The specific color fixing agent preparation process steps are as follows:
[0091] Step 1: Stir ammonium chloride and diethylenetriamine at a speed of 700r / min for 25min, heat up to 100°C, and keep warm for 1h to obtain mixture a;
[0092] Step 2: Add dicyandiamide and ethylene glycol to mixture A, raise the temperature to 130° C., and keep the temperature for 30 minutes to obtain mixture b;
[0093] Step 3: when the temperature of the mixture B is lowered to 90°C, add water and glacial acetic acid to obtain the mixture c;
[0094] Step 4: Add sodium hydroxide, nano-chitin, gelatin, sodium caseinate and carrageenan to mixture C, and stir for 15 minutes at a rotational speed of 900 r / min to obtain mixture d, which is the color-fixing agent.
[0095] Wherein, the weight part that sodium caseinate adds is as shown in table 3:
...
PUM
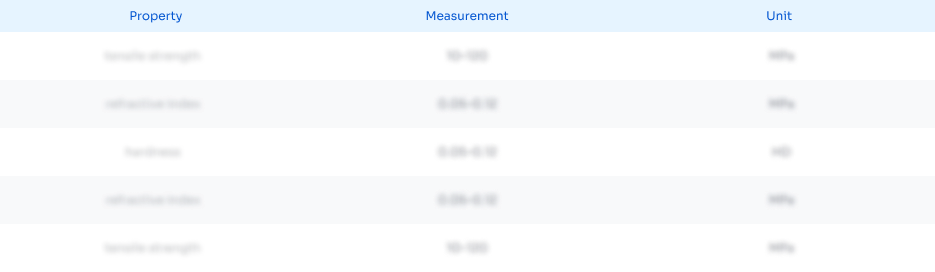
Abstract
Description
Claims
Application Information

- R&D
- Intellectual Property
- Life Sciences
- Materials
- Tech Scout
- Unparalleled Data Quality
- Higher Quality Content
- 60% Fewer Hallucinations
Browse by: Latest US Patents, China's latest patents, Technical Efficacy Thesaurus, Application Domain, Technology Topic, Popular Technical Reports.
© 2025 PatSnap. All rights reserved.Legal|Privacy policy|Modern Slavery Act Transparency Statement|Sitemap|About US| Contact US: help@patsnap.com