An energy-saving bionic tension-compression body patellofemoral joint for bipedal walking robot
A technology of walking robots and hip joints, applied in manipulators, motor vehicles, joints, etc., can solve problems such as complex control algorithms, complex algorithms, and energy consumption, so as to increase joint stability, reduce energy consumption, and increase lever arm Effect
- Summary
- Abstract
- Description
- Claims
- Application Information
AI Technical Summary
Problems solved by technology
Method used
Image
Examples
Embodiment Construction
[0045] The present invention is described below in conjunction with accompanying drawing.
[0046] Such as figure 1 As shown, the present invention is composed of a bionic double ball member A, a bionic sliding lever member B, a ligament assembly C and a connector 1, wherein: the connector I is fixedly connected to the upper end of the bionic double ball member A; the bionic sliding lever member B is located on the bionic double ball The front end of the ball component A, the connector I is fixedly connected to the upper end of the bionic double ball component A; the lower end of the flexible bionic patella ligament 16 of the ligament component C is screwed to the upper part of the matrix threaded hole group V11 on the front surface of the bionic sliding lever component B via bolts The upper end of the flexible bionic patella inferior ligament 17 is threadedly connected to the lower part of the matrix threaded hole group V11 at the front end of the bionic sliding lever member ...
PUM
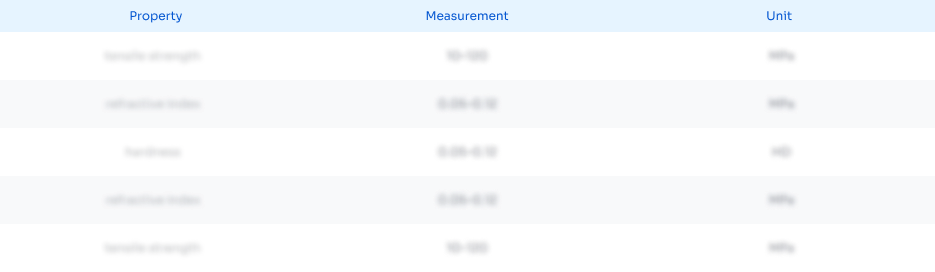
Abstract
Description
Claims
Application Information

- Generate Ideas
- Intellectual Property
- Life Sciences
- Materials
- Tech Scout
- Unparalleled Data Quality
- Higher Quality Content
- 60% Fewer Hallucinations
Browse by: Latest US Patents, China's latest patents, Technical Efficacy Thesaurus, Application Domain, Technology Topic, Popular Technical Reports.
© 2025 PatSnap. All rights reserved.Legal|Privacy policy|Modern Slavery Act Transparency Statement|Sitemap|About US| Contact US: help@patsnap.com