Method for extracting vanadium from vanadium titano-magnetite smelting slag through roasting and ultrasonic leaching
A technology of vanadium-titanium magnetite and smelting slag, which is applied in the field of metallurgy and can solve problems such as large consumption of sulfuric acid
- Summary
- Abstract
- Description
- Claims
- Application Information
AI Technical Summary
Problems solved by technology
Method used
Examples
Embodiment 1
[0032] The method for extracting vanadium by roasting and ultrasonic leaching of smelting slag of vanadium-titanium magnetite specifically comprises the following steps:
[0033] (1) Crushing the vanadium-titanium magnetite smelting slag, drying, and ball milling until the particle size is 80-100 mesh and accounting for more than 90wt%, according to the solid-liquid mass ratio of 1g: 1ml in the ball mill, add a mass percentage of 15 % sulfuric acid solution;
[0034] (2) Add 0.02wt% additive (the additive in this example is a mixture of limestone and KCl, with a mass ratio of 1:1) and 0.3wt% hydrogen peroxide to the pretreated vanadium-titanium magnetite smelting slag, Roast at 600°C, hold for 0.5h;
[0035] (3) Add 0.1wt% ferric sulfate in the roasted material, mix evenly, wet the material with water, the addition of water is 8wt% of the vanadium-titanium magnetite smelting slag;
[0036] (4) Add 0.8wt% concentrated sulfuric acid to the material in step (3), ultrasonicate w...
Embodiment 2
[0038] The method for extracting vanadium by roasting and ultrasonic leaching of smelting slag of vanadium-titanium magnetite specifically comprises the following steps:
[0039] (1) Crushing the vanadium-titanium magnetite smelting slag, drying, and ball milling until the particle size is 80-100 mesh and accounting for more than 90wt%, according to the solid-liquid mass ratio of 1g: 1ml in the ball mill, add a mass percentage of 15 % sulfuric acid solution;
[0040] (2) Add 0.02wt% additive (the additive in this example is a mixture of limestone, NaF and KCl, with a mass ratio of 1:1:1) and 0.5wt% oxidant in the pretreated vanadium-titanium magnetite smelting slag Potassium permanganate, roasted at 650°C and kept for 0.5h;
[0041] (3) Add 0.2wt% potassium sulfate to the roasted material, mix evenly, and wet the material with water, and the addition of water is 10wt% of the vanadium-titanium magnetite smelting slag;
[0042] (4) Add 0.5wt% concentrated sulfuric acid to the ...
Embodiment 3
[0044] The method for extracting vanadium by roasting and ultrasonic leaching of smelting slag of vanadium-titanium magnetite specifically comprises the following steps:
[0045] (1) Vanadium-titanium-magnetite smelting slag is crushed, dried, and ball milled to a particle size of 80 to 100 mesh, accounting for more than 90wt%. During the ball milling process, the mass percentage of 30% sulfuric acid solution;
[0046] (2) Add 0.04wt% additive (the additive in this embodiment is a mixture of limestone, NaF and KCl, with a mass ratio of 1:1:1) and 0.4wt% oxidizing agent in the vanadium-titanium magnetite smelting slag after pretreatment Potassium permanganate, roasted at 700°C and kept for 0.2h;
[0047] (3) Add 0.2wt% ferrous sulfate in the roasted material, mix evenly, wet the material with water, the addition of water is 12wt% of the vanadium-titanium magnetite smelting slag;
[0048] (4) Add 0.25wt% concentrated sulfuric acid to the material in step (3), ultrasonicate for...
PUM
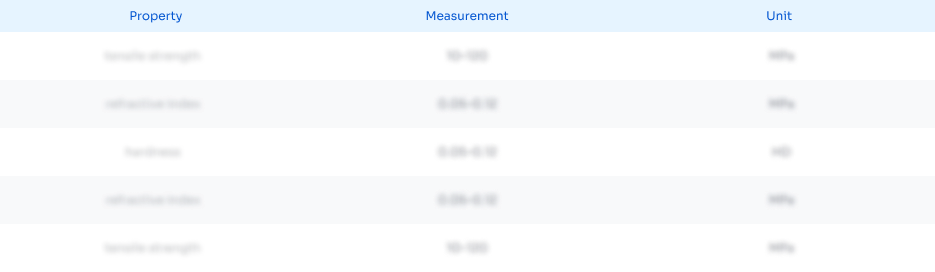
Abstract
Description
Claims
Application Information

- R&D
- Intellectual Property
- Life Sciences
- Materials
- Tech Scout
- Unparalleled Data Quality
- Higher Quality Content
- 60% Fewer Hallucinations
Browse by: Latest US Patents, China's latest patents, Technical Efficacy Thesaurus, Application Domain, Technology Topic, Popular Technical Reports.
© 2025 PatSnap. All rights reserved.Legal|Privacy policy|Modern Slavery Act Transparency Statement|Sitemap|About US| Contact US: help@patsnap.com