Track geometrical morphology detection device
A technology of geometric shape and detection device, which is applied in the direction of measuring device, optical device, surveying and navigation, etc., can solve the problems of large investment of manpower, difficulty in equipment erection, inability to measure the height difference of double-track gauge and double-track at the same time, and smoothness of single track, etc.
- Summary
- Abstract
- Description
- Claims
- Application Information
AI Technical Summary
Problems solved by technology
Method used
Image
Examples
Embodiment Construction
[0033] The track geometry detection device of the present invention is as Figure 18 As shown, it includes two reference light sources, a gauge detection vehicle and an elevation detection vehicle. The two reference light sources are placed on the two measured rails. On the track to be tested, there is a wireless communication connection between the gauge detection vehicle and the elevation detection vehicle.
[0034] Such as Figure 1-4 As shown, a reference light source laser 7 is installed inside the front side of the reference light source casing 1 of the reference light source, and a reference light source laser emission port 2 is provided on the quasi-light source casing 1 corresponding to the reference light source laser 7, and a reference light source lithium is installed in the reference light source casing 1. Battery 9, reference light source driving board 10 and reference light source control main board 13, reference light source lithium battery 9 is connected to r...
PUM
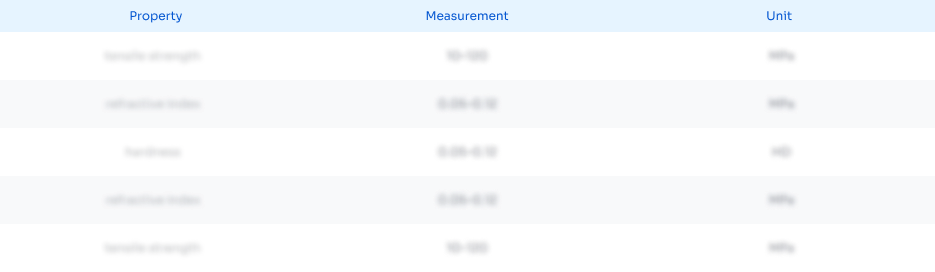
Abstract
Description
Claims
Application Information

- R&D Engineer
- R&D Manager
- IP Professional
- Industry Leading Data Capabilities
- Powerful AI technology
- Patent DNA Extraction
Browse by: Latest US Patents, China's latest patents, Technical Efficacy Thesaurus, Application Domain, Technology Topic, Popular Technical Reports.
© 2024 PatSnap. All rights reserved.Legal|Privacy policy|Modern Slavery Act Transparency Statement|Sitemap|About US| Contact US: help@patsnap.com