Metal modified Y-type molecular sieve and preparation method thereof
A metal modification and molecular sieve technology, which is applied in the directions of fajhedral crystalline aluminosilicate zeolite and crystalline aluminosilicate zeolite, etc., can solve the problems of loss of metal elements and limiting the application of metal modified Y-type molecular sieves.
- Summary
- Abstract
- Description
- Claims
- Application Information
AI Technical Summary
Problems solved by technology
Method used
Image
Examples
Embodiment 1
[0025] The method of the present invention prepares metal-modified Y-type molecular sieve samples
[0026] (1) Mix 100 grams of NaY molecular sieve (dry basis) with 400 grams of deionized water, make a slurry, raise the temperature to 90°C, adjust the pH of the resulting slurry system to ≈4.5 with dilute hydrochloric acid, and then add 0.5 grams of CTAB and 5.37 grams of hexahydrate in sequence Metal chloride (containing 2 g M 2 o 3 ), and continued stirring for 1 hour.
[0027] (2) Adjust the pH of the slurry system obtained in the above step (1) to ≈7 with ammonia solution, continue to stir and react for 5 minutes, then filter, wash, dry and perform water vapor ultra-stabilization treatment.
[0028] (3) The molecular sieve sample obtained in step (2) was mixed with ammonium chloride salt solution, beaten, and subjected to ammonium ion exchange, and then filtered, washed and dried to obtain the metal-modified Y-type molecular sieve sample C1.
Embodiment 2
[0030] The method of the present invention prepares metal-modified Y-type molecular sieve samples
[0031] (1) Mix 100 grams of NaY molecular sieve (dry basis) with 1000 grams of deionized water, make a slurry, raise the temperature to 60°C, adjust the pH of the resulting slurry system to ≈3 with dilute hydrochloric acid, then add 3 grams of CTAB and 21.49 grams of hexahydrate in sequence Metal chloride (containing 8 grams of M 2 o 3 ), and continued to stir for 4 hours.
[0032] (2) Adjust the pH of the slurry system obtained in the above step (1) to 6.5 with ammonia solution, continue to stir and react for 30 minutes, then filter, wash, dry and perform water vapor ultra-stabilization treatment.
[0033] (3) Mix the molecular sieve sample obtained in step (2) with the ammonium chloride salt solution, beat, perform ammonium ion exchange, and then filter, wash and dry to obtain the metal-modified Y-type molecular sieve sample C2.
Embodiment 3
[0035] The method of the present invention prepares metal-modified Y-type molecular sieve samples
[0036](1) Mix 100 grams of NaY molecular sieve (dry basis) with 600 grams of deionized water, make a slurry, heat up to 80°C, adjust the pH of the resulting slurry system to ≈4 with dilute hydrochloric acid, and then add 1 gram of CTAB and 10.75 grams of hexahydrate in sequence Metal chloride (containing 4 g M 2 o 3 ), and continued to stir for 2 hours.
[0037] (2) Adjust the pH of the slurry system obtained in the above step (1) to ≈8 with ammonia solution, continue to stir and react for 10 minutes, then filter, wash, dry and perform water vapor ultra-stabilization treatment.
[0038] (3) Mix the molecular sieve sample obtained in step (2) with the ammonium chloride salt solution, make a slurry, perform ammonium ion exchange, and then filter, wash and dry to obtain the metal-modified Y-type molecular sieve sample C3.
PUM
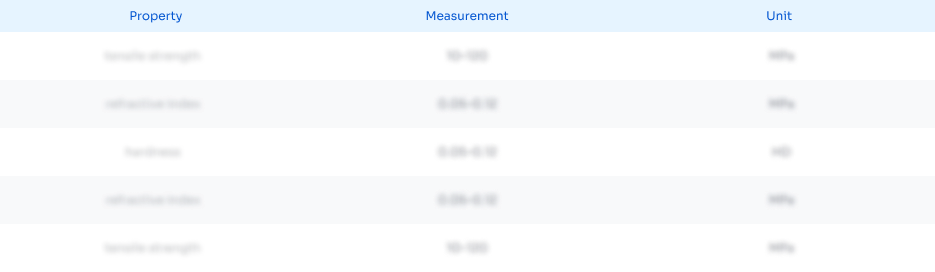
Abstract
Description
Claims
Application Information

- R&D Engineer
- R&D Manager
- IP Professional
- Industry Leading Data Capabilities
- Powerful AI technology
- Patent DNA Extraction
Browse by: Latest US Patents, China's latest patents, Technical Efficacy Thesaurus, Application Domain, Technology Topic, Popular Technical Reports.
© 2024 PatSnap. All rights reserved.Legal|Privacy policy|Modern Slavery Act Transparency Statement|Sitemap|About US| Contact US: help@patsnap.com