A Multi-stage Dynamic Continuously Adjustable Variable Moment of Inertia Hydraulic Retarder Test Bench
A technology of hydraulic retarder and moment of inertia, which is used in the testing of mechanical parts, the testing of machine/structural components, and the testing of machine gears/transmission mechanisms, etc. Use efficiency and other issues, to ensure the test accuracy and use efficiency, to avoid the effect of multiple disassembly and assembly
- Summary
- Abstract
- Description
- Claims
- Application Information
AI Technical Summary
Problems solved by technology
Method used
Image
Examples
Embodiment 1
[0033] Example 1: Simulation of the braking performance of the hydraulic retarder on a continuously changing ramp condition
[0034] When it is necessary to simulate the braking performance of the hydraulic retarder in the uphill working condition of the vehicle, firstly, the combination of the governor clutch is controlled by the hydraulic control device, and an inertia disc 4 that is not rigidly connected with the main shaft is passed through the governor gear 9 Realize rigid connection with the speed regulating shaft; then, the electronic control unit adjusts the speed regulating motor 10 to the same speed as the main motor 1 according to the speed data measured by the speed sensor on the main motor 1 and the speed regulating motor 10, at this time It can be considered that the inertial disc 4 cooperating with the speed regulating gear 9 is at the same speed as the main shaft. The electronic control unit dynamically and continuously changes the oil pressure of the system ac...
Embodiment 2
[0036] Example 2: Simulation of the braking performance of the hydraulic retarder in continuous shifting conditions
[0037] When simulating the braking performance of the hydraulic retarder in continuous shifting conditions, since the increase coefficient of the rotating mass changes before and after shifting, the overall moment of inertia of the test bench should also have a corresponding value during the simulation test. Variety. Due to the short time of the shifting process, it can be approximately regarded as a sudden change in the moment of inertia in the test simulation. When it is necessary to simulate the shifting process to increase or decrease the moment of inertia of the test bench, the operation steps are the same as when simulating the braking efficiency of the hydraulic retarder under the uphill or downhill conditions of the vehicle, but the electronic control unit has a certain influence on the system. The oil pressure control should make the inertia disc clut...
PUM
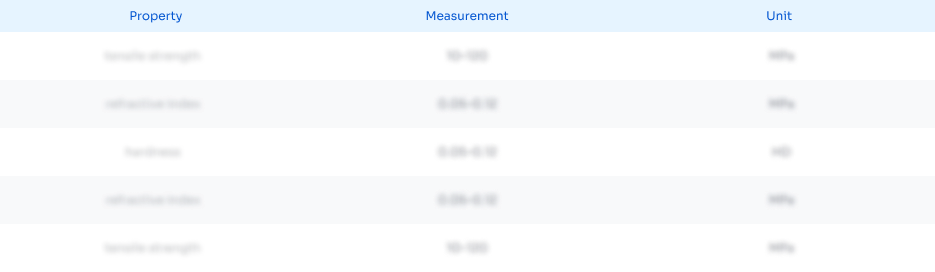
Abstract
Description
Claims
Application Information

- R&D
- Intellectual Property
- Life Sciences
- Materials
- Tech Scout
- Unparalleled Data Quality
- Higher Quality Content
- 60% Fewer Hallucinations
Browse by: Latest US Patents, China's latest patents, Technical Efficacy Thesaurus, Application Domain, Technology Topic, Popular Technical Reports.
© 2025 PatSnap. All rights reserved.Legal|Privacy policy|Modern Slavery Act Transparency Statement|Sitemap|About US| Contact US: help@patsnap.com