Cast iron material for automobile manifold and automobile manifold
A technology for manifolds and automobiles, applied in the direction of casting molds, casting mold components, casting molding equipment, etc., can solve the problems of low fuel combustion efficiency and low power
- Summary
- Abstract
- Description
- Claims
- Application Information
AI Technical Summary
Problems solved by technology
Method used
Image
Examples
Embodiment 1
[0034] The present embodiment provides a kind of automobile manifold, comprises the following steps:
[0035] 1) Design as figure 1 As shown in the left manifold mold, according to the chemical mass percentage of each component of the cast iron material, it is 3.0% carbon, 4% silicon, 0.6% manganese, 0.8% molybdenum, 0.08% magnesium, and the balance is iron and unremovable impurities. Prepare raw materials ;
[0036] 2) heating the raw materials with a good ratio to a molten state, this step can adopt the process of melting raw materials in the existing process;
[0037] 3) Pre-furnace spectrum detection chemical composition ratio;
[0038] 4) making sand cores, casting molding: making sand cores through the mold obtained in step 1), and then pouring the molten solution in step 2) into the sand cores, casting molding;
[0039] 5) According to the machining process required by the manifold tooling;
[0040] 6) Finished product packaging.
Embodiment 2
[0042] The present embodiment provides a kind of automobile manifold, comprises the following steps:
[0043] 1) Design as figure 2 For the right manifold mold shown, according to the chemical mass percentage of each component of the cast iron material, it is 3.4% carbon, 5% silicon, 0.35% manganese, 1.1% molybdenum, 0.28% magnesium, and the balance is iron and unremovable impurities. Prepare raw materials ;
[0044] 2) heating the raw materials with a good ratio to a molten state, this step can adopt the process of melting raw materials in the existing process;
[0045] 3) Pre-furnace spectrum detection chemical composition ratio;
[0046] 4) making sand cores, casting molding: making sand cores through the mold obtained in step 1), and then pouring the molten solution in step 2) into the sand cores, casting molding;
[0047] 5) According to the machining process required by the manifold tooling;
[0048] 6) Finished product packaging.
Embodiment 3
[0050] The present embodiment provides a kind of automobile manifold, comprises the following steps:
[0051] 1) Design as figure 1 As shown in the left manifold mold, according to the chemical mass percentage of each component of the cast iron material, it is 3.22% carbon, 4.75% silicon, 0.3% molybdenum, 0.01% magnesium, and the balance is iron and non-removable impurities. Raw materials are prepared;
[0052] 2) heating the raw materials with a good ratio to a molten state, this step can adopt the process of melting raw materials in the existing process;
[0053] 3) Pre-furnace spectrum detection chemical composition ratio;
[0054] 4) making sand cores, casting molding: making sand cores through the mold obtained in step 1), and then pouring the melt in step 2) into the sand cores, casting molding;
[0055] 5) According to the machining process required by the manifold tooling;
[0056] 6) Finished product packaging.
PUM
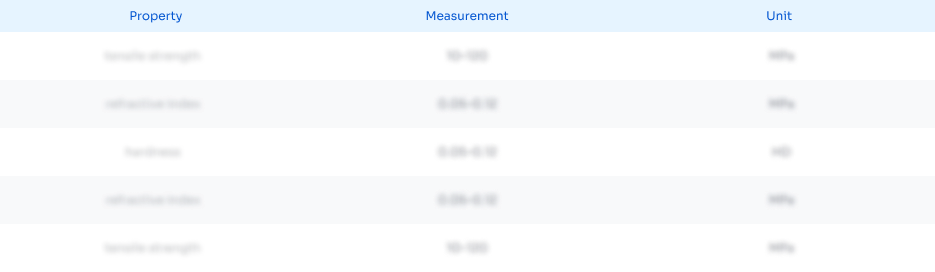
Abstract
Description
Claims
Application Information

- R&D Engineer
- R&D Manager
- IP Professional
- Industry Leading Data Capabilities
- Powerful AI technology
- Patent DNA Extraction
Browse by: Latest US Patents, China's latest patents, Technical Efficacy Thesaurus, Application Domain, Technology Topic, Popular Technical Reports.
© 2024 PatSnap. All rights reserved.Legal|Privacy policy|Modern Slavery Act Transparency Statement|Sitemap|About US| Contact US: help@patsnap.com