Three-dimensional vibration-assisted milling processing system and three-dimensional vibration-assisted milling method for structural surface
A three-dimensional vibration and milling processing technology, which is applied in the direction of metal processing equipment, milling machine equipment, manufacturing tools, etc., can solve the problem that the processing accuracy and processing efficiency of structural surface are difficult to improve at the same time, and achieve the reduction of crack propagation, small processing force, and smooth surface. The effect of high integrity
- Summary
- Abstract
- Description
- Claims
- Application Information
AI Technical Summary
Problems solved by technology
Method used
Image
Examples
Embodiment 1
[0056] Three-dimensional vibration-assisted milling processing systems, including CNC machine tools and three-dimensional vibration-assisted devices8, such as figure 1 As shown, the CNC machine tool includes an X-direction slide rail 1, a Y-direction slide rail 2 and a Z-direction slide rail 3 at the top, and a Z-direction shaft 10 and a Y-direction shaft 11 at the bottom, wherein:
[0057] The X-direction slide rail 1 and the Y-direction slide rail 2 are perpendicular to each other, and the Z-direction slide rail 3 is driven to move horizontally along the X-direction slide rail 1 in the X-axis direction, and along the Y-direction slide rail 2 Move horizontally in the Y-axis direction, the processing assembly is driven to move horizontally along the Z-direction slide rail 3 in the Z-axis direction, and the processing assembly includes a driving mechanism, a main shaft 4 driven to rotate by the driving mechanism, and a Tool 5 on spindle 4;
[0058] The workpiece 6 is fixed on ...
Embodiment 2
[0062] In the three-dimensional vibration-assisted milling processing system of Embodiment 1, a coordinate system is established. There are three coordinate systems: machining system coordinate system, workpiece coordinate system and tool coordinate system.
[0063] (1) Coordinate system of processing system:
[0064]The coordinate system of the processing system is represented by O-XYZ, which is based on the center of the machine tool table as the origin, the X axis is parallel to the X-direction slide rail of the machine tool, the Y axis is parallel to the machine tool Y-direction slide rail, and the Z axis is parallel to the machine tool Z-direction slide rail.
[0065] (2) Workpiece coordinate system:
[0066] O for workpiece coordinate system W -X W Y W Z W Indicates that the origin is located at a certain point of the workpiece, X W axis, Y W axis, Z W The axes are all parallel to the X, Y, and Z axes in the machining system coordinate system.
[0067] (3) Tool ...
Embodiment 3
[0070] A three-dimensional vibration-assisted milling method for a structural surface, comprising the following steps:
[0071] Define the tool coordinate system as O T -X T Y T Z T , define the workpiece coordinate system as O W -X W X W Z W .
[0072] Step 1, in the tool coordinate system, the surface topography equation of the modeling tool is:
[0073]
[0074] In the formula (1), the x T , y T ,z T is the coordinate of any point on the tool surface in the tool coordinate system, denoted as C T Point coordinates, R is the tool surface C T The distance from the point to the tool axis, θ is O T C T in X T O T Y T Surface projection and X T The angle of the axis.
[0075] In the formula (1), when the tool shape is spherical with radius r, R takes the value rsinφ, where The value of r is 1 during simulation.
[0076] Step 2, in the workpiece coordinate system, establish the surface topography equation of the workpiece as:
[0077] F(x w , y w ,z ...
PUM
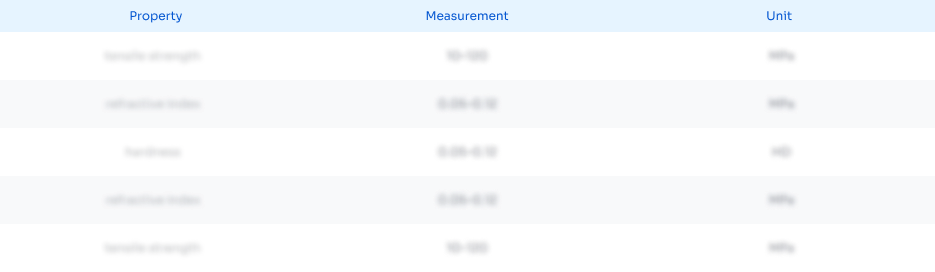
Abstract
Description
Claims
Application Information

- Generate Ideas
- Intellectual Property
- Life Sciences
- Materials
- Tech Scout
- Unparalleled Data Quality
- Higher Quality Content
- 60% Fewer Hallucinations
Browse by: Latest US Patents, China's latest patents, Technical Efficacy Thesaurus, Application Domain, Technology Topic, Popular Technical Reports.
© 2025 PatSnap. All rights reserved.Legal|Privacy policy|Modern Slavery Act Transparency Statement|Sitemap|About US| Contact US: help@patsnap.com