Three-dimensional vibration-assisted milling system and structural surface three-dimensional vibration-assisted milling method
A three-dimensional vibration and milling processing technology, which is applied in the direction of metal processing equipment, milling machine equipment, manufacturing tools, etc., can solve the problems that the machining accuracy and machining efficiency of structural surfaces are difficult to improve at the same time, and achieve the reduction of crack growth, high operating accuracy, and smooth processing. small force effect
- Summary
- Abstract
- Description
- Claims
- Application Information
AI Technical Summary
Problems solved by technology
Method used
Image
Examples
Embodiment 1
[0056] Three-dimensional vibration-assisted milling processing system, including CNC machine tools and three-dimensional vibration auxiliary devices8, such as figure 1 As shown, the CNC machine tool includes an X-direction slide rail 1, a Y-direction slide rail 2, and a Z-direction slide rail 3 at the top, and a Z-direction rotating shaft 10 and a Y-direction rotating shaft 11 at the bottom, wherein:
[0057] The X-direction slide rail 1 is perpendicular to the Y-direction slide rail 2, and the Z-direction slide rail 3 is driven to move horizontally along the X-direction slide rail 1 in the X-axis direction, and moves along the Y-direction slide rail 2 Moving horizontally in the Y-axis direction, the processing assembly is driven to move horizontally in the Z-axis direction along the Z-direction slide rail 3. The processing assembly includes a driving mechanism, a main shaft 4 driven by the driving mechanism and fixed on the Tool 5 on spindle 4;
[0058] The workpiece 6 is fi...
Embodiment 2
[0062] In the three-dimensional vibration-assisted milling system of Embodiment 1, a coordinate system is established. There are three coordinate systems in total: processing system coordinate system, workpiece coordinate system and tool coordinate system.
[0063] (1) Processing system coordinate system:
[0064]The coordinate system of the processing system is represented by O-XYZ, which is based on the center of the machine table as the origin, the X-axis is parallel to the X-direction slide rail of the machine tool, the Y-axis is parallel to the Y-direction slide rail of the machine tool, and the Z-axis is parallel to the Z-direction slide rail of the machine tool.
[0065] (2) Workpiece coordinate system:
[0066] The workpiece coordinate system uses O W -X W Y W Z W Indicates that the origin is located at a certain point on the workpiece, X W Axis, Y W Axis, Z W The axes are all parallel to the X-axis, Y-axis, and Z-axis in the coordinate system of the machining ...
Embodiment 3
[0070] A three-dimensional vibration-assisted milling method for a structured surface, comprising the following steps:
[0071] Define the tool coordinate system as O T -X T Y T Z T , define the workpiece coordinate system as O W -X W x W Z W .
[0072] Step 1. In the tool coordinate system, the surface topography equation of the modeling tool is:
[0073]
[0074] In the formula (1), the x T ,y T ,z T is the coordinate of any point on the tool surface in the tool coordinate system, denoted as C T Point coordinates, R is tool surface C T The distance from the point to the tool axis, θ is O T C T at x T o T Y T Surface Projection and X T Angle of the axis.
[0075] In the formula (1), when the shape of the tool is spherical with a radius of r, the value of R is rsinφ, where The value of r is 1 during simulation.
[0076] Step 2, in the workpiece coordinate system, the surface topography equation of the workpiece is established as:
[0077] F(x w ,y ...
PUM
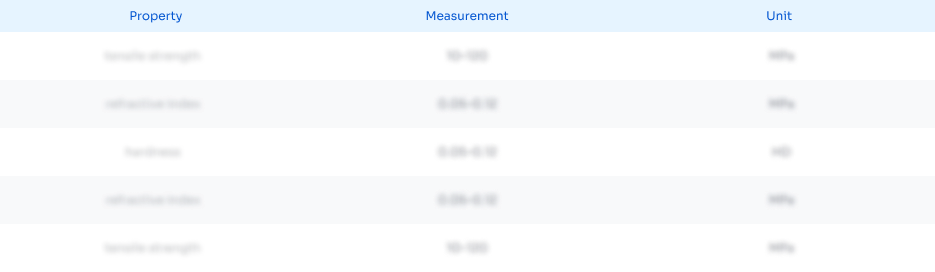
Abstract
Description
Claims
Application Information

- Generate Ideas
- Intellectual Property
- Life Sciences
- Materials
- Tech Scout
- Unparalleled Data Quality
- Higher Quality Content
- 60% Fewer Hallucinations
Browse by: Latest US Patents, China's latest patents, Technical Efficacy Thesaurus, Application Domain, Technology Topic, Popular Technical Reports.
© 2025 PatSnap. All rights reserved.Legal|Privacy policy|Modern Slavery Act Transparency Statement|Sitemap|About US| Contact US: help@patsnap.com