Micromechanical detection structure and MEMS inertial measurement device
A detection structure, micro-mechanical technology, applied in the field of MEMS devices, to achieve the effects of reducing stress mismatch, improving thermal drift, and reducing the radius of rotation
- Summary
- Abstract
- Description
- Claims
- Application Information
AI Technical Summary
Problems solved by technology
Method used
Image
Examples
Embodiment Construction
[0029] In order to make the technical problems, technical solutions and beneficial effects to be solved by the present invention clearer, the present invention will be further described in detail below in conjunction with the accompanying drawings and embodiments. It should be understood that the specific embodiments described here are only used to explain the present invention, not to limit the present invention.
[0030] Please also refer to figure 1 and figure 2 , the micromechanical detection structure provided by the present invention will now be described. The micromechanical detection structure includes a central anchor point 1, a connecting beam, a vibration mass 2, a fixed electrode 3 and a movable electrode 4. The central anchor point 1 is used to be fixed on the substrate 5, and one end of the connecting beam is fixedly connected to the central anchor point 1. The other end protrudes to the outside of the central anchor point 1; the vibrating mass 2 has a frame-s...
PUM
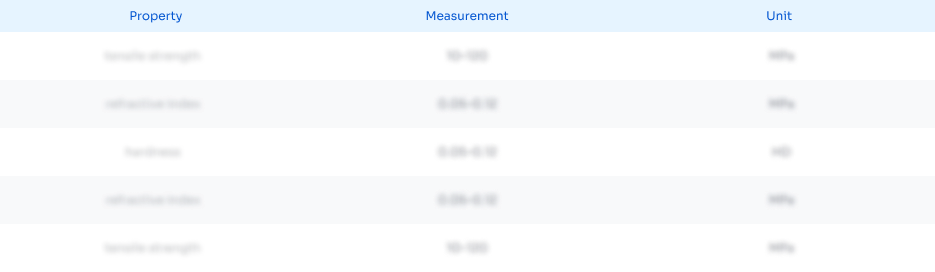
Abstract
Description
Claims
Application Information

- Generate Ideas
- Intellectual Property
- Life Sciences
- Materials
- Tech Scout
- Unparalleled Data Quality
- Higher Quality Content
- 60% Fewer Hallucinations
Browse by: Latest US Patents, China's latest patents, Technical Efficacy Thesaurus, Application Domain, Technology Topic, Popular Technical Reports.
© 2025 PatSnap. All rights reserved.Legal|Privacy policy|Modern Slavery Act Transparency Statement|Sitemap|About US| Contact US: help@patsnap.com