A method for automatic identification of damaged areas of aerospace composite materials
A composite material and aerospace technology, applied in the field of aerospace vehicle damage detection and maintenance support, can solve the problems of misjudgment of defect identification, large quantity, vulnerability to the environment, imaging links, etc., and achieve the effect of strong applicability
- Summary
- Abstract
- Description
- Claims
- Application Information
AI Technical Summary
Problems solved by technology
Method used
Image
Examples
Embodiment
[0232]In this embodiment, the infrared thermal imaging camera collected 502 frames of images with a pixel size of 512×640. That is, there are 327,680 temperature points on each map, and the temperature value of each temperature point is recorded 502 times. This time-varying temperature condition constitutes the transient thermal response TTR of the temperature point. Step 1: After extracting the effective transient thermal response from the infrared thermal sequence, divide the area according to the defect type, and extract the typical transient thermal response from each type of divided area. When extracting the effective transient thermal response, set the parameter Re CL =0.92, 375 valid transient thermal responses containing complete defect information were extracted from 327,680 temperature points. According to the pixel points, the membership degree of each cluster center is softened, and 185, 43 and 147 thermal response curves are divided into corresponding categorie...
PUM
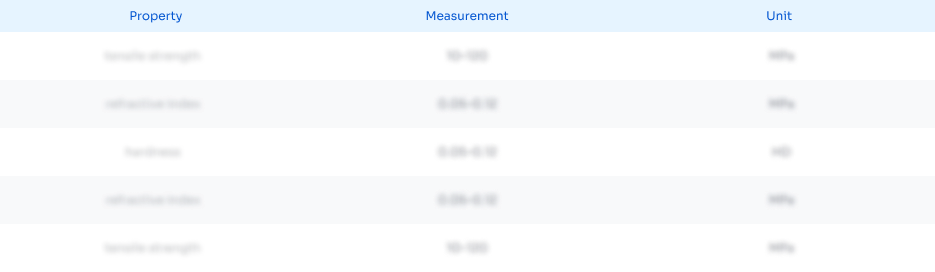
Abstract
Description
Claims
Application Information

- R&D Engineer
- R&D Manager
- IP Professional
- Industry Leading Data Capabilities
- Powerful AI technology
- Patent DNA Extraction
Browse by: Latest US Patents, China's latest patents, Technical Efficacy Thesaurus, Application Domain, Technology Topic, Popular Technical Reports.
© 2024 PatSnap. All rights reserved.Legal|Privacy policy|Modern Slavery Act Transparency Statement|Sitemap|About US| Contact US: help@patsnap.com