Induction heating tempering treatment method
A technology of induction heating and treatment method, applied in the field of roll manufacturing, can solve problems such as difficulty in local tempering treatment, and achieve the effects of reducing heat treatment energy consumption, reducing production costs, and strong operability
- Summary
- Abstract
- Description
- Claims
- Application Information
AI Technical Summary
Problems solved by technology
Method used
Examples
Embodiment 1
[0023] A treatment method for induction heating and tempering, the requirements for the work roll are as follows:
[0024] Roll specification: ¢520 / 490×1200×2850, unit weight: 3.05 tons;
[0025] Main roll neck¢340×430 Hardness requirement: HSD55-65;
[0026] Roll material: alloy forged steel;
[0027] Using electric furnace smelting + ladle refining + electroslag remelting, the steel ingot is heated and forged according to the process requirements to make a roll forging billet, and then the roll is induction quenched.
[0028] Temper the main roll neck ¢340×430 (hardness in the quenched state HSD80-95) to meet the corresponding hardness requirements. The specific steps are as follows:
[0029] A, the roll after the quenching treatment rotates at a speed of 15 rpm;
[0030] B. Conduct induction heating and tempering: conduct induction heating and tempering on the main roll neck, the final target heating temperature is 580°C, the operating speed of the electromagnetic induct...
Embodiment 2
[0033] The difference between this embodiment and Embodiment 1 is that the induction heating and tempering in step B operates in four stages, and the operating temperatures of the four stages are 150°C, 300°C, 450°C, and 580°C, respectively.
Embodiment 3
[0035] The difference between this example and Example 1 is that the induction heating tempering in Step B is run in ten stages, and the operating temperatures of the ten stages are 150°C, 200°C, 250°C, 300°C, 350°C, 400°C, 450°C, 500°C, 550°C, 580°C.
PUM
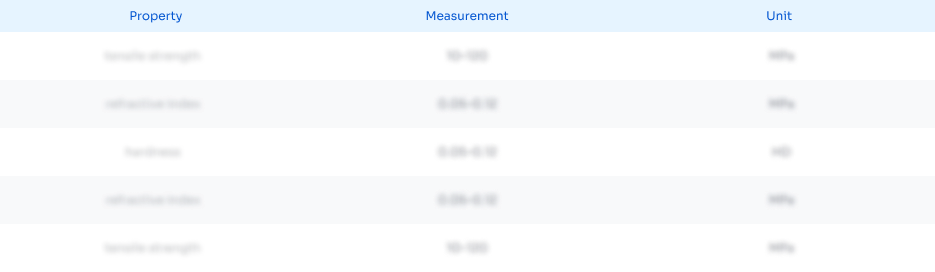
Abstract
Description
Claims
Application Information

- R&D Engineer
- R&D Manager
- IP Professional
- Industry Leading Data Capabilities
- Powerful AI technology
- Patent DNA Extraction
Browse by: Latest US Patents, China's latest patents, Technical Efficacy Thesaurus, Application Domain, Technology Topic, Popular Technical Reports.
© 2024 PatSnap. All rights reserved.Legal|Privacy policy|Modern Slavery Act Transparency Statement|Sitemap|About US| Contact US: help@patsnap.com