Novel oil tank support manufactured based on magnesium alloy and manufacturing process of novel oil tank support
A magnesium alloy bracket and magnesium alloy technology, applied in the field of automobile manufacturing, can solve the problems of low convenience and flexibility, fuel tank bracket structure, complicated forming and installation steps, and inability to disassemble.
- Summary
- Abstract
- Description
- Claims
- Application Information
AI Technical Summary
Problems solved by technology
Method used
Image
Examples
Embodiment 1
[0040]Such asFigure 2-6 As shown, the present embodiment provides a novel fuel tank holder based on a magnesium alloy, including a magnesium alloy bracket body 1, and the magnesium alloy bracket body 1 is a reaction "L" type corner structure. The two side surfaces of the magnesium alloy bracket body 1 form a plurality of grooves 2, and between adjacent grooves 2 constitute a reinforcing thus 3, and the reinforcing thus is constituted by digging the raw material, not only the overall weight of the stent is not only. Moreover, the fuel tank holder is greatly reduced while increasing the effective cross-sectional area; wherein the reinforcing ribs 3 are plate-shaped reinforcing thumbers. Both ends of the magnesium alloy bracket body 1 are provided with a jack 4 for a strap through which a strap (not shown) is used to secure the fuel tank on the magnesium alloy bracket body 1. The above-mentioned reinforcing ribs 3, the jack 4, and the magnesium alloy bracket body 1 are die casting inte...
Embodiment 2
[0048]This embodiment provides a manufacturing process based on the new fuel tank holder according to the embodiment, mainly including the steps of:
[0049]Step S1: Meliite the magnesium alloy particles or magnesium ingots into liquid magnesium alloys;
[0050]Step S2: Pour the liquid magnesium alloy into the molded mold of the die casting machine;
[0051]Step S3: Start the die casting machine, integrally molded the magnesium alloy material by die from the magnesium alloy bracket body 1, and the magnesium alloy bracket body 1 includes a recess 2, a reinforcing rib 3, a jack 4, and aperture 5.
[0052]Unlike the conventional fuel tank stent process, the novel fuel tank holder made of magnesium alloy based in this example uses a die-casting integrated molding process, and the cross-sectional area of the die-casting fuel tank holder is larger, and the unit cross-sectional area can be reduced when weighing. The force has enabled the original strength in the case where the material is weak, and ...
PUM
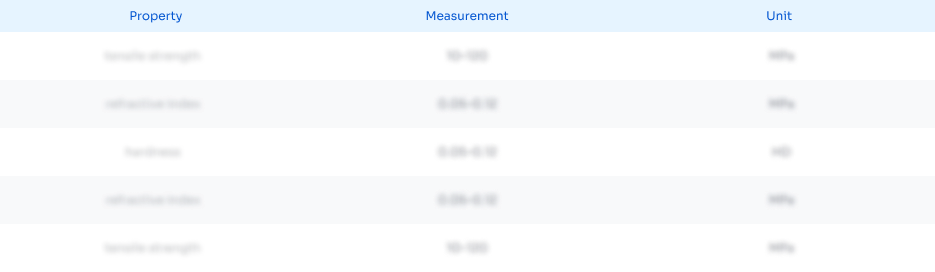
Abstract
Description
Claims
Application Information

- R&D Engineer
- R&D Manager
- IP Professional
- Industry Leading Data Capabilities
- Powerful AI technology
- Patent DNA Extraction
Browse by: Latest US Patents, China's latest patents, Technical Efficacy Thesaurus, Application Domain, Technology Topic, Popular Technical Reports.
© 2024 PatSnap. All rights reserved.Legal|Privacy policy|Modern Slavery Act Transparency Statement|Sitemap|About US| Contact US: help@patsnap.com