Method for producing zinc oxide for ceramic glaze by using hot-dip galvanized ash
A ceramic glaze and zinc oxide technology, applied in the direction of zinc oxide/zinc hydroxide, etc., can solve problems such as serious corrosion of smelting equipment, achieve good environmental protection benefits, good economic benefits, and reduce production costs
- Summary
- Abstract
- Description
- Claims
- Application Information
AI Technical Summary
Problems solved by technology
Method used
Image
Examples
Embodiment 1
[0043] Embodiment 1: choose 30 hot-dip galvanizing plants zinc ash (galvanized pipe ash) comprehensive samples in Daqiuzhuang, Jinghai District, Tianjin, its zinc ash detects each component content (quality) to be respectively: Zn% is 62.14, and Pb% is 0.34, Al 2 o 3 % is 6.8%, As%2 %<0.5, CaO% is 0.11, MgO% is 0.029, Cu% is 0.011, Ni% is 0.025, Fe% is 0.40, K% is 0.016, Mn% is 0.041, Hg%<0.0005.
[0044] The preparation steps of zinc oxide are:
[0045] S1: wet ball milling
[0046] Take 500g of the sample, grind it with a small ball mill until 80% pass through a 150 mesh sieve, and control the water consumption of the ball mill at 2000ml;
[0047] S2: Filtration to remove iron
[0048]Filter and remove iron from the ball-milled slurry of S1 with a slurry iron remover;
[0049] S3: wet dechlorination
[0050] Add the iron-removed slurry in step S2 into the reaction kettle, stir, the stirrer rotates at 150r / min, add 70g of sodium hydroxide (NaOH), heat to a temperature o...
Embodiment 2
[0053] Embodiment 2: Select the galvanized pipe ash of a galvanizing plant in Yuxi, Yunnan, and its zinc ash detects that the contents (mass) of each component are respectively: Zn% is 66.51, Cl% is 12.54, ZnCO 3 % is 2.31, Fe% is 0.41, Pb% is 0.32, Cd% is 0.03, S% is 0.21, Al 2 o 3 % is 2.15. This plant produces part of the powdered metal zinc powder when plating thin tubes. The Zn% of this metal powder is 97.1%, and the C1% is 0.35. Element content is relatively high.
[0054] The preparation steps of zinc oxide are:
[0055] S1: wet ball milling
[0056] Take 500g of the sample, grind it with a small ball mill until 80% pass through a 150 mesh sieve, and control the water consumption of the ball mill at 2000ml;
[0057] S2: Filtration to remove iron
[0058] Filter and remove iron from the ball-milled slurry of S1 with a slurry iron remover;
[0059] S3: wet dechlorination
[0060] Add the iron-removed slurry in step S2 into the reaction kettle and stir at a stirrer...
Embodiment 3
[0063] Embodiment 3: choose a certain galvanizing plant tube ash in Baoding, Hebei, its zinc ash detects each component content (quality) to be respectively: Zn% is 55.18, Cl% is 14.52, Fe% is 0.25, Pb% is 0.38, Cd% is 0.48, S% is 0.23, Al 2 o 3 % is 8.78.
[0064] The preparation steps of zinc oxide are:
[0065] S1: wet ball milling
[0066] Take 500g of the sample, grind it with a small ball mill until 80% pass through a 150 mesh sieve, and control the water consumption of the ball mill at 2500ml;
[0067] S2: Filtration to remove iron
[0068] Filter and remove iron from the ball-milled slurry of S1 with a slurry iron remover;
[0069] S3: wet dechlorination
[0070] Add the slurry after iron removal in step S2 into the reaction kettle, stir, the stirrer speed is 100r / min, add 90gNa 2 CO 3 , heated to a temperature of 95°C, and reacted for 1.5 hours. Filtration and dehydration, the filter cake is washed with distilled water until the mass content of Cl ions is les...
PUM
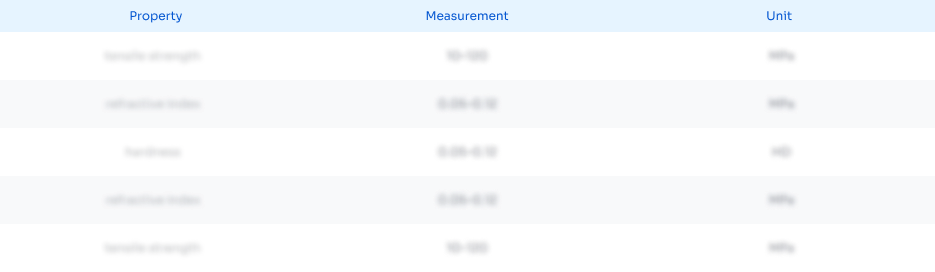
Abstract
Description
Claims
Application Information

- R&D
- Intellectual Property
- Life Sciences
- Materials
- Tech Scout
- Unparalleled Data Quality
- Higher Quality Content
- 60% Fewer Hallucinations
Browse by: Latest US Patents, China's latest patents, Technical Efficacy Thesaurus, Application Domain, Technology Topic, Popular Technical Reports.
© 2025 PatSnap. All rights reserved.Legal|Privacy policy|Modern Slavery Act Transparency Statement|Sitemap|About US| Contact US: help@patsnap.com