Multidirectional spraying system and spraying process based on glass bottle production
A multi-directional technology for glass bottles, applied in coatings, spray booths, spraying devices, etc., can solve problems such as non-environmental protection, waste of paint, and lengthening the processing time of glass bottles
- Summary
- Abstract
- Description
- Claims
- Application Information
AI Technical Summary
Problems solved by technology
Method used
Image
Examples
Embodiment 1
[0045] Embodiment one: if Figure 1-14 As shown, a multi-directional spraying system based on glass bottle production includes a mounting base 1. Two symmetrically arranged drive rollers 2 are installed on the top of the mounting base 1. One side of the mounting base 1 is provided with a driving drive roller. 2 The driving assembly that rotates at the same time, the outer sides of the two transmission rollers 2 are connected to the same conveyor belt 7, and the top of the conveyor belt 7 is equidistantly arranged with a plurality of glass bottles 9, and the top of the conveyor belt 7 is equipped with multiple The positioning holes 8 are arranged equidistantly in the horizontal direction, and the positioning holes 8 and the glass bottles 9 are compatible. When the glass bottles 9 fall into the designated positioning holes 8 through the feeding pipe 17, the positioning holes 8 can be used to improve the glass bottle. The stable performance of the bottle 9 movement, the top of th...
Embodiment 2
[0058] Embodiment two: if Figure 15 As shown, a multi-directional spraying system based on the production of glass bottles, the difference between this embodiment and Embodiment 1 is that: the discharge assembly 47 includes a discharge seat 4701, and the top of the discharge seat 4701 is provided with a strip-shaped transportation groove, and the transportation A plurality of transport rollers 4702 are rotatably connected to the inner wall of the bottom of the trough, and the plurality of transport rollers 4702 are connected by transmission. One side of the discharge seat 4701 is fixedly connected with two rotating cylinders 4704 arranged symmetrically. Two rotating rollers 4703 arranged symmetrically are rotationally connected, and the rotating rollers 4703 and the conveying rollers 4702 are connected by transmission. The second sprocket 4706 is fixedly installed on the center of one side of the rotating rollers 4703, and the output shaft of the rotating cylinder 4704 is fixe...
PUM
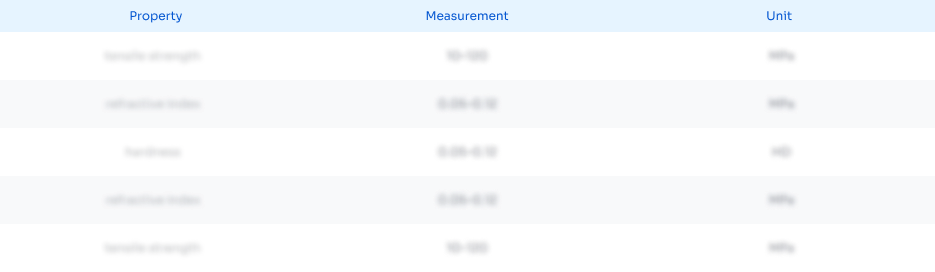
Abstract
Description
Claims
Application Information

- R&D
- Intellectual Property
- Life Sciences
- Materials
- Tech Scout
- Unparalleled Data Quality
- Higher Quality Content
- 60% Fewer Hallucinations
Browse by: Latest US Patents, China's latest patents, Technical Efficacy Thesaurus, Application Domain, Technology Topic, Popular Technical Reports.
© 2025 PatSnap. All rights reserved.Legal|Privacy policy|Modern Slavery Act Transparency Statement|Sitemap|About US| Contact US: help@patsnap.com