Fixed bed hydrogenation reactor and heavy oil liquid phase hydrogenation process
A hydrogenation reactor and hydrogenation reaction technology are applied in the petrochemical field and can solve the problems of high activity and large temperature rise.
- Summary
- Abstract
- Description
- Claims
- Application Information
AI Technical Summary
Problems solved by technology
Method used
Image
Examples
Embodiment 1
[0039] Attached figure 1 In the described method, the catalyst I packed in the inner cylinder of the heavy oil hydrogenation reactor adopts the FZC protective agent / FF-46 catalyst developed by the Fushun Petrochemical Research Institute, wherein the FZC protective agent is 15% of the total catalyst volume of the outer cylinder, and the annular area The packed catalyst II adopts the 3936 catalyst developed by Fushun Petrochemical Research Institute.
[0040] The hydrogen contained in the raw material oil in the feed of the heavy oil hydrogenation reactor is 3.66% of the mass of the raw material oil (the sum of fresh raw material oil and cycle oil); The sum of raw oil and circulating oil) is 9.28% of the mass; the circulation ratio is 2.5.
[0041] The reaction conditions of the inner cylinder of the hydrogenation reactor are as follows: the reaction temperature is 384-403°C, the reaction pressure is 15.0MPaG, and the liquid hourly volume space velocity is 2.8h -1 ;The reactio...
Embodiment 2
[0045] Attached figure 1 In the described method, the catalyst I filled in the inner cylinder of the heavy oil hydrogenation reactor adopts the FZC protective agent / 3996 catalyst developed by the Fushun Petrochemical Research Institute, wherein the FZC protective agent is 15% of the total catalyst volume of the outer cylinder, and the annular area is filled Catalyst II uses 3936 catalyst developed by Fushun Petrochemical Research Institute.
[0046] The hydrogen contained in the raw material oil in the feed of the heavy oil hydrogenation reactor is 5.40% of the mass of the raw material oil (the sum of fresh raw material oil and cycle oil); The sum of raw oil and circulating oil) is 7.74% of the mass; the circulation ratio is 2.0.
[0047] The reaction conditions of the inner cylinder of the hydrogenation reactor are as follows: the reaction temperature is 382-401°C, the reaction pressure is 15.0MPaG, and the liquid hourly volume space velocity is 2.2h -1 ;The reaction condit...
Embodiment 3
[0051] Attached figure 1 In the described method, the catalyst I packed in the inner cylinder of the heavy oil hydrogenation reactor adopts the FZC protective agent / FF-46 catalyst developed by the Fushun Petrochemical Research Institute, wherein the FZC protective agent is 15% of the total catalyst volume of the outer cylinder, and the annular area The packed catalyst II adopts FF-16 catalyst developed by Fushun Petrochemical Research Institute.
[0052] The hydrogen contained in the raw material oil in the feed of the heavy oil hydrogenation reactor is 7.66% of the mass of the raw material oil (the sum of fresh raw material oil and cycle oil); The sum of raw oil and circulating oil) is 5.28% of the mass; the circulation ratio is 2.0.
[0053] The reaction conditions of the inner cylinder of the hydrogenation reactor are as follows: the reaction temperature is 385-404°C, the reaction pressure is 15.0MPaG, and the liquid hourly volume space velocity is 2.0h -1 The reaction co...
PUM
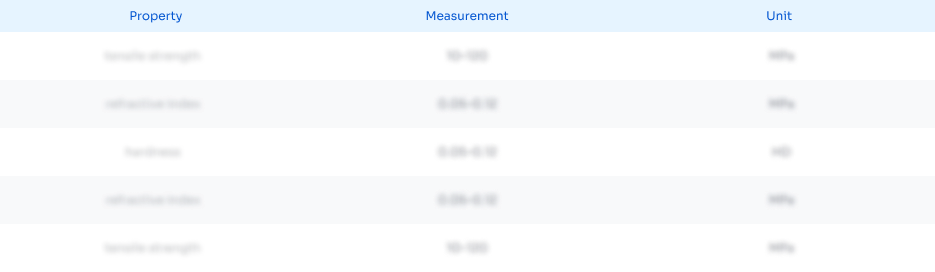
Abstract
Description
Claims
Application Information

- R&D
- Intellectual Property
- Life Sciences
- Materials
- Tech Scout
- Unparalleled Data Quality
- Higher Quality Content
- 60% Fewer Hallucinations
Browse by: Latest US Patents, China's latest patents, Technical Efficacy Thesaurus, Application Domain, Technology Topic, Popular Technical Reports.
© 2025 PatSnap. All rights reserved.Legal|Privacy policy|Modern Slavery Act Transparency Statement|Sitemap|About US| Contact US: help@patsnap.com